
3D printed Wye with a Gentler Slope and a Dart Ramp
#26
Posted 04 April 2013 - 04:11 PM
I'm going to be making a few prototypes for a 22-1/2 degree Wye out of Delrin or Aluminum for testing purposes sometime soon. If it works well with Streamlines and Elite then I can look into either making a bunch using CNC to make these out of grey PVC, or casting them out of clear urethane.
Cast parts will have a tooling cost, but the per-part price will probably be half the cost of having to machine them.
#27
Posted 04 April 2013 - 04:43 PM
#28
Posted 04 April 2013 - 10:46 PM
'CaptainSlug', on 04 Apr 2013 - 9:11 PM, said:
Every company I've contacted about Injection molding wants nearly $10,000 to pay for tooling. For how much they're asking I could just pay for a whole at-home injection molding setup.
I'm going to be making a few prototypes for a 22-1/2 degree Wye out of Delrin or Aluminum for testing purposes sometime soon. If it works well with Streamlines and Elite then I can look into either making a bunch using CNC to make these out of grey PVC, or casting them out of clear urethane.
Cast parts will have a tooling cost, but the per-part price will probably be half the cost of having to machine them.
I hope your plan was not to make them square like that. It just doesn't look good. You probably knew that, your smart.

#29
Posted 04 April 2013 - 11:47 PM
'quertyman', on 05 Apr 2013 - 03:46 AM, said:
What's wrong with making them square? With the exception of injection molding, almost any manufacturing process is easier on square parts.I hope your plan was not to make them square like that. It just doesn't look good. You probably knew that, your smart.
Kruger and Dunning (1999)
#30
Posted 05 April 2013 - 09:44 AM
'quertyman', on 05 Apr 2013 - 03:46 AM, said:
Only the inside geometry of the part is terribly important for it to function. Making it rounded would add more time and cost to the prototype.I hope your plan was not to make them square like that. It just doesn't look good. You probably knew that, your smart.
Casting one of these is going to require a 5-part mold. 3 tools for the internal geometry and 2 mold halves for the outside. I'll probably have to make a pneumatic extractor tool for removing the internal tools from the part after they're freed from the mold.
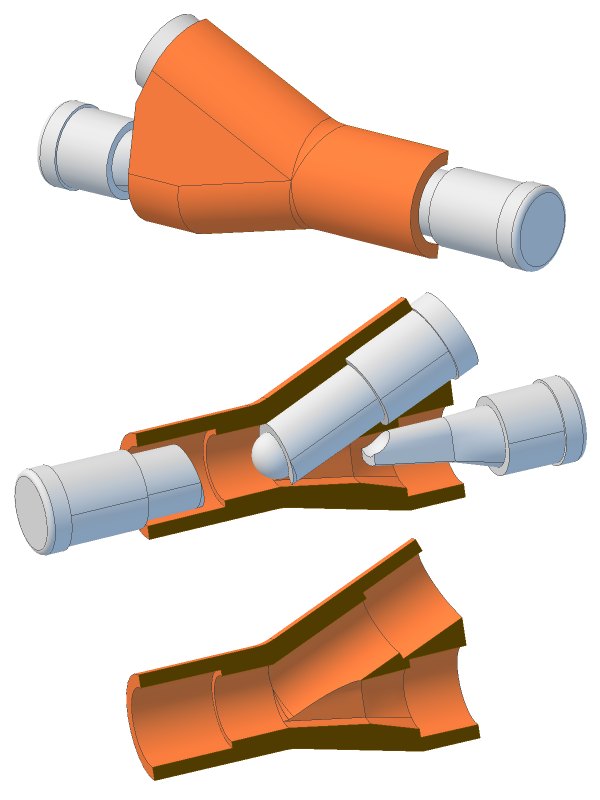
It's only shown as Orange so you can see the inside surface.
#31
Posted 05 April 2013 - 10:37 AM
Edited by Ivan S, 05 April 2013 - 10:41 AM.
~Talio
#32
Posted 05 April 2013 - 11:36 AM
Maybe I should just consider making the wye in two halves then PVC Cementing them together. That way I can make much smoother internal geometries.
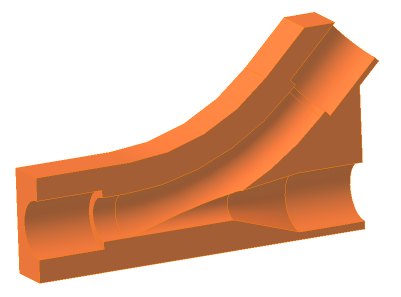
'Ivan S', on 05 Apr 2013 - 3:37 PM, said:
So long as the area of the passageway doesn't decrease too much below the area of the back of a dart I don't see how it will have an impact. I made the passageway larger between the first drawing I posted and the most recent image.Do you think the air inlet being thinner than normal could decrease performance?
#33
Posted 05 April 2013 - 01:26 PM
'CaptainSlug', on 05 Apr 2013 - 4:36 PM, said:
I thought of that also, but it probably won't be a problem because the vibration of firing a springer, running, and priming or pumping any blaster will most likely shake the darts enough to cause them to feed correctly. The biggest issue may be what you mentioned before—the hopper ramming into the blaster's plunger tube.One potential complication I see with having a shallower angle is that the darts have less assistance from gravity to feed down the dart hopper.
#34
Posted 05 April 2013 - 02:26 PM
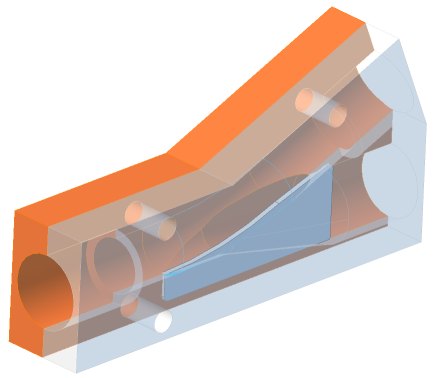
The other nice side effect of making this in two halves is that I can use the prototype as a mold to make the casting for the production mold.
#35
Posted 05 April 2013 - 04:46 PM
Anyway that you can send me a copy of the design that I could print on a 3D printer?
#36
Posted 05 April 2013 - 05:30 PM
'CaptainSlug', on 05 Apr 2013 - 4:36 PM, said:
So long as the area of the passageway doesn't decrease too much below the area of the back of a dart I don't see how it will have an impact. I made the passageway larger between the first drawing I posted and the most recent image.
Makes sense. KaneTheMediocre made a 3D printed wye in two parts like that. It fires silicone head darts, but I'm not sure on the details since he only made the one post about it. Maybe you could contact him.
~Talio
#37
Posted 05 April 2013 - 09:44 PM
'Ivan S', on 05 Apr 2013 - 10:30 PM, said:
Makes sense. KaneTheMediocre made a 3D printed wye in two parts like that. It fires silicone head darts, but I'm not sure on the details since he only made the one post about it. Maybe you could contact him.
Ryan's actually been working on a new 1-piece wye, and I really think that's the way to go. The two-piece avoids any overhang, but getting the seam to seal well and have the ports still fit is not a trivial matter. My wye, which I THINK had a 25 degree angle, required hot-glue around the seam, drilling out the ports with a spade bit, and then hot-gluing in the clip, barrel, and air input. We've been printing his prototypes (all of which haven't turned out well enough to be worth testing) with the clip facing up (ish) rather than with the wye on it's side.
The challenge really has a lot more to do with the quality of print than the design of the wye. My printer isn't tuned particularly well, even by by the low standards of homebuilt filament printers, so most inside walls aren't smooth enough to guide darts in. The low-angle wye worked in part because it had geometry that my printer could do smoothly. If you're getting parts from Shapeways or other business-class printers, you can probably get away with a lot more.
#38
Posted 06 April 2013 - 10:28 AM
First off, 3D printing this part through a service like Shapeways will be too expensive due to the volume of the part. You would be looking at $30-$40 per part.
3D printing at home would require a lot of extra effort to get working parts.
Machining these out of gray PVC is expedient for me since I can do it from work. Doing them in large quantities may not be feasible though and the per-part price will meet the target.
Injection molding involves more equipment than I'm willing to buy. I also can't injection mold PVC at home because of off-gassing and the need for stainless steel tooling.
Casting is attractive because I can keep the part price well below $10. The resulting parts will probably be white or clear polyurethane. I just have to pick a geometry that works and that I can produce through casting.
And the primary challenges with streamlines are the rubber tip and long length.
#39
Posted 06 April 2013 - 11:51 AM
'CaptainSlug', on 06 Apr 2013 - 3:28 PM, said:
Casting is attractive because I can keep the part price well below $10. The resulting parts will probably be white or clear polyurethane. I just have to pick a geometry that works and that I can produce through casting.
Beware, Ryan and I went partway down that road. We had a mold for handles, and a 2-piece design for casting wyes, but the handles that we made were quite brittle. We tried a couple different types of polyurethane mixes with similar results. I'm not saying that there isn't something out there (maybe even some kind of polyurethane) that will work and be reasonably durable, but producing good parts will probably require some experimentation with different materials.
#40
Posted 09 April 2013 - 08:25 AM
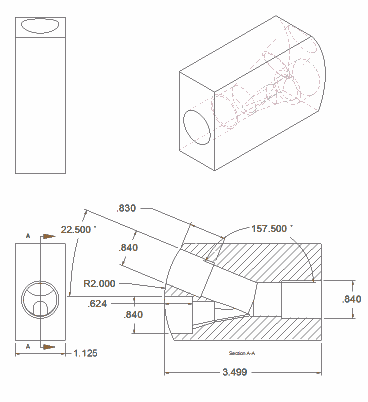
#41
Posted 09 April 2013 - 11:29 AM
'KaneTheMediocre', on 06 Apr 2013 - 02:44 AM, said:
The challenge really has a lot more to do with the quality of print than the design of the wye. My printer isn't tuned particularly well, even by by the low standards of homebuilt filament printers, so most inside walls aren't smooth enough to guide darts in. The low-angle wye worked in part because it had geometry that my printer could do smoothly. If you're getting parts from Shapeways or other business-class printers, you can probably get away with a lot more.
Have you considered using the printed part(s) to just be a housing for PVC tubes and/or a jig for cutting them to the correct angles? So in the end you wouldn't be using the printed part to do anything other than hold the tubing used in the right places.
Or, since the overall goal is rapid-fire streamline dart capability, perhaps a new mag system could be designed using 3d printed parts and easy to get tubing? I've got a design floating around for a belt system that would be easy to produce given some 3d printed or cast parts.
#42
Posted 09 April 2013 - 05:17 PM
Quote
Or, since the overall goal is rapid-fire streamline dart capability, perhaps a new mag system could be designed using 3d printed parts and easy to get tubing? I've got a design floating around for a belt system that would be easy to produce given some 3d printed or cast parts.
What be the concept behind this belt system?
#43
Posted 09 April 2013 - 06:05 PM
'Kronos Nerf Mods', on 09 Apr 2013 - 10:17 PM, said:
What be the concept behind this belt system?
The machine gun belt feed mech animation on How Stuff Works was the original inspiration, I had an epiphany looking at Captain Slug's old Sledgehammer plans and realized that the frame and pins used to move the mag could be replaced with a slightly more complex mechanism, allowing the mag to just be a bunch of barrel-tubes cut to length and duct taped together (at a specific spacing, but again, 3d Printing a spacer for assembling these would be a cinch).
I'm PM'ing you the rest because I cannot link images for some reason.
#44
Posted 09 April 2013 - 07:53 PM
Would using a 3/4" wye give more room to help darts chamber and bend through the wye ?
#45
Posted 10 April 2013 - 10:55 AM
'lech', on 10 Apr 2013 - 12:53 AM, said:
If you are going to fuck around loading belts and what-not, why not just use N-Strike clips?
Mainly because N-strike/elite clips require breaches, which have a tendency to jam. A belt would allow a much higher number of darts to be carried than in any clip, and any type of dart to be used if the belt system was designed for it. If it was made into a loop, it'd also allow reloading on the fly; it'd basically just be a flexible turret.
#46
Posted 10 April 2013 - 02:45 PM
'Meaker VI', on 10 Apr 2013 - 3:55 PM, said:
Mainly because N-strike/elite clips require breaches, which have a tendency to jam. A belt would allow a much higher number of darts to be carried than in any clip, and any type of dart to be used if the belt system was designed for it. If it was made into a loop, it'd also allow reloading on the fly; it'd basically just be a flexible turret.
If it is going to be like a turret then you are essentially making a chain-blazer. One disadvantage of using chains would be carrying capacity, if you have 3 chains of 100 rounds each (one in the blaster, two on your vest or belt) you would have chains swinging around and it would be heavy. Even if you compacted them they would take up a lot of space. With a hopper/RCSB you could have the same 300 darts is a pouch or bandolier that would be 1/2 the weight and you could shove darts in several at a time, rather than reloading a whole chain.
Now, because this thread was started on hoppers, I think we should post about the original subject, not on potential reloading mechanisms.
I like Slug's design with the sliver of plastic to direct the dart, but I think we can print it in 1 piece or mod current wyes with wire or zip tie.
If we are going to make custom wyes, why not incorporate special features. Instead of going from PVC to ramp, why not incorporate a funnel to take advantage of the Venturi effect?
Or make holders on the side for extra barrels so if one gets jammed, you can switch it fast and not worry about clearing the jam until you are in a safe zone or after the battle?
Edited by Super0dp, 10 April 2013 - 02:47 PM.
#47
Posted 22 April 2013 - 05:08 PM
How to make Silicone Domes
#48
Posted 23 April 2013 - 04:47 PM
How to make Silicone Domes
#49
Posted 23 April 2013 - 06:51 PM
Still can't believe that its feeding elite darts. I had never tried, but I had always assumed that they wouldn't work.
#50
Posted 23 April 2013 - 07:33 PM
0 user(s) are reading this topic
0 members, 0 guests, 0 anonymous users