Note: this is a proof of concept, with refinements to come later. So, let's get this turkey roasting, shall we?
A glamour shot of what may be the least glamourous SNAP ever.
Functionally, it's very similar to the SNAP/Revolution, but has a few differences as far as operation. Here's a side-on view:
And now a version with 87% more exploded view:
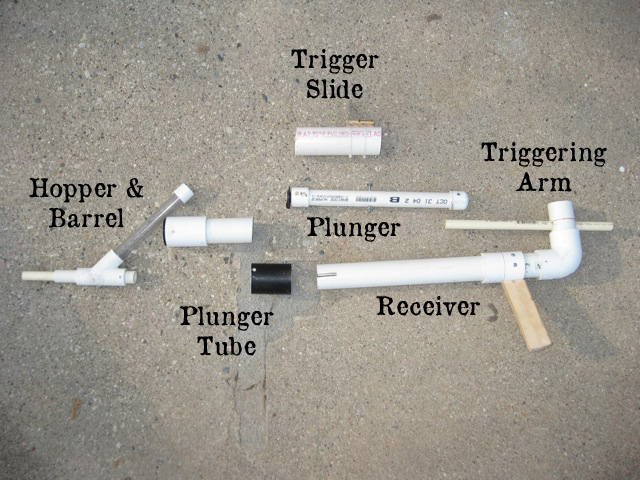
Now then, on to the parts...
The Receiver:
You can see the slot in the top where the firing pin slides. The slots in the front are for the forward spring stop in the plunger. These slots are in the plunger tube on the SNAP/Revolution. The triggering arm is what actuates the trigger on the trigger slide. It's ugly, but functional (I built it using the first three scraps I could find (the arm is 1/2" CPVC, shoved through a hole in a chunk of 1.25" PVC, in a 1.25" elbow).
The Plunger:
Here's the biggest difference from the SNAP-9: The catchface is on the end of the plunger (like the SNAP-PAC and the SNAP-8), and the spring is tensioned inside of the plunger tube (as opposed to being hung from the receiver on one end, and the plunger tube on the other end).
The plunger assembly then just drops into the receiver.
The Charging Slide:
The charging slide is made of 1.5" thinwall, which slides perfectly over 1.25" PVC (thanks to SomethingNerfey for hooking me up!). I was a little surprised that it has enough wall thickness to support a CPT directly, but hey. I'm not going ot argue with success. It's a typical clothespin trigger. The nail rides in the slot on the receiver. Push it forward, and the CPT will engage the rear of the plunger tube. Pull the charging slide back, and the plunger goes along for the ride. When it meets the triggering arm:
The extra bit in front of the handle clip is there as a travel stop, so the slide can't over-extend and pop out the nail. Future versions could just have a longer charging slide.
The Hopper, Barrel & Plunger Tube:
Not much to be said here. The plunger tube currently attaches with a screw, but could also use the SNAP/Rev tool-less plunger tube clip method.
Assembly:
It breaks down and assembles quite easily:
1. Slide the plunger tube into the receiver.
2. Lift the CPT, and slide it onto the receiver until the nail clicks into the top slot on the receiver.
3. Press the plunger tube/barrel assembly into place, and screw down.
Questions:
Q: So, what kind of range does it get?
A: For a proof of concept, Far Enough. I didn't take any accurate measurements, and it's hard to fire a slamfire flat. Estimating, I was spamming darts about 60 feet.
Q: How fast does it fire?
A: I can empty the five shot hopper in under three seconds, arrived at by a highly scientific method of counting "one-one thousand, two-one thousand"...
Q: How strong is that spring?
A: Not exactly sure. The spring in the SNAP/Rev is about 14 pounds, and this one is far weaker. I'd guess...8 pounds?
Q: Isn't a five shot hopper sorta useless for a slamfire gun?
A: This is a proof of concept. Future builds will use a larger spring, will be able to use a larger hopper, and will probably get better range.
Q: That triggering arm doesn't look very stable.
A: The current shape was built for easy adjustments and tuning. Even so, I put a few hundred darts through it this afternoon, and it never shifted on me.
Q: That thing's really ugly, like it got hit in the head with a really ugly thing.
A: She may not look like much, but she's got it where it counts, kid.