You will need the following.
Tools
Dremel
Drill (drill press would help)
Scroll saw/Band saw
Etape
Lube
6/32 Tap
Solvent Weld
Goop
Materials:
2' Piece of 1 1/4" PVC
1x 4" Piece of 1 1/4" PVC
1x 1 1/4" PVC Tee
1x 1 1/4" PVC Coupler
2x 3/4" PVC Endcaps
1x 1" to 1/2" PVC Bushing
1x 3/4" to 1/2" Reducing Bushing
1' Piece of 1/2" PVC
1x 1/2" PVC Stub (~2")
1x 1/2" PVC Endcap
1x 1/2" PVC Elbow
1x 3/4" ID Rubber O-ring
16x 6/32 Machine Screws of varying size
2x Wood Screws
1x Plunger Head setup (I use 3/4" steel, 1 1/2" rubber, 1 1/4" rubber, 1 1/4" steel, in that order)
1x 1/2" CPVC Endcap
1x 1/2" CPVC coupler
5" Piece of 1/2" CPVC
1x Vertical Handle
1x Pump Handle (could be a vertical handle too)
1x [k25] spring (or [k26], though you may have to change the measurements)
1x PVC Wye and hopper setup
5x Polycarb parts of varying size/shape
1x A chunk of 2" PVC (sort of optional)
Preparing the Main Body
From the start pick an end that will be the front. Then mark a slot starting 1/2" from the front and continuing for 9", the width of the slot was determined by the Polycarb I used (3/8"). I like putting it on the area with print so I never have to see it if I don't paint it.


Then on the exact opposite side of the tube I drilled a 5/8" hole directly in the middle (12" from the front)

That's all that needs to be done for now.
The Handle
This will use the vertical handle, the 1 1/4" coupler and the wood screws. First I drilled holes through the coupler about an inch apart then widened two of them such that a screwdriver could fit through, then I carefully lined up, marked and drilled pilot holes into the handle.

(The material you use may not require this)
Before final assembly I put goop where the coupler and handle would n=meet to make it a but stronger. Here it is finished.

The Stock
This will use the 1 1/4" Tee, one of the 3/4" Endcaps a bit of etape and the 5" section of 1 1/4" PVC.
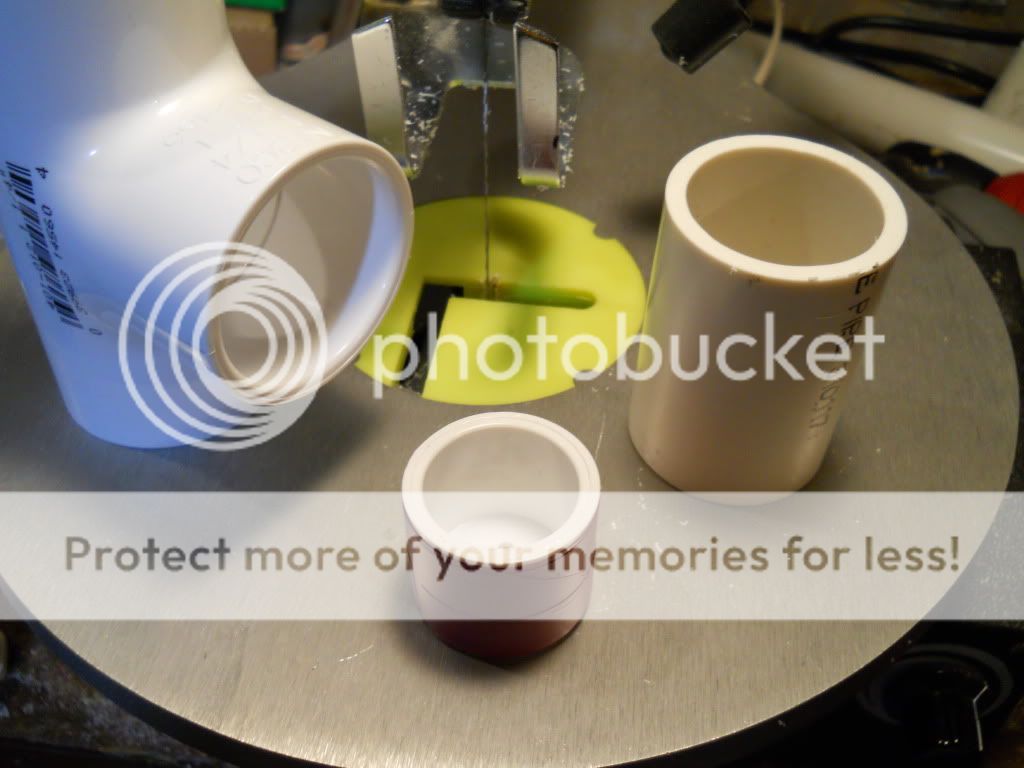
Drill some holes in the endcap, tape it up and combine like so:

It doesn't show it but you will want to put screws through this part as it will be the spring rest.
I then solvent welded this part into the back of the coupler to which the handle is attached, you can use screws for a less totally permanent option.
The Pump Handle Assembly
This will use the Pump grip/handle, the 1' of 1/2" PVC, the 3/4" ID O-ring, a polycarb rectangle 3/4" by 2 1/2" and the 1/2" PVC endcap.
First chose an end of the PVC and do this with the endcap and O-ring

Next on the other end mark the PVC, rectangle and handle/grip.

I attempted to stagger the holes to reduce stress of the parts as much as possible (also gives more room for error).
(I would simplify this if I had longer screws)

Dissemble for a future step, or trust that it'll work in final assembly, whatever.
Back to the Main Body
Take the 1" to 1/2" bushing and ream out the inside so it slides over 1/2" PVC easily (I ended up lubing it a little to prevent galling between the parts) also dremel the outside so it just barely fits in the 1 1/4" PVC of the main body. This part will fit in the ~1 1/2" gap between the hole drilled earlier and the end of the slot. I drilled a hole so I could solvent weld it in place, as an added measure I also put screws into but not through these parts.


Final position, sort of hard to tell (I should make one of these out of clear PVC)

If you have any issues with the parts not fitting quite as well after assembly tape some sandpaper to a long piece of CPVC and fix it by sanding 'til it works.
I inserted the 1/2" PVC part of the pump bar marked where holes should be drilled so the pump could be reassembled inside the main body, then did so.

I inserted the 3/4" to 1/2" reducing bushing into the remaining 3/4" endcap, cut it in half and put the cap end on the end of the pump bar. Save the other half.

I cut and sanded the 1/2" PVC elbow to fit over the 5/8" drill hole on the main body and the other half of the endcap-reducing bushing thing to slide over 1/2" PVC

Solvent welded in place, make sure it's strait. It's important.

Plunger Rod
This will use the CPVC parts and the plunger head setup.

The rearmost thing is half of the coupler, it will hold the catchface in place, it needs to be a few inches back because the spring is a little shorter than optimal. All parts are solvent welded together. If you use a clothespin trigger you will need to figure that out on your own, in fact the nuances of catching are sort of ad-lib anyway, just do whatever you want; HEC's are magic anyway.
Back to the Handle
I cut polycarb parts as needed

as well as cut a bit out of the main body for the HEC catch.
and assembled, added a spring

Here you can see one of the screws I used to attach the two sections together after inserting the necessary parts (spring, plungerrod). I used the chunk of 2" PVC here as a cheek rest, it is a lot more comfortable than the edge of a coupler.

And that should be all you need to make a complete blaster.
Note; I'm not telling how to make a HEC catch because they have a tendency to not really work all that well and newer nerfers would probably not have the tools necessary. The one shown works absolutely perfectly, I'm just not sure how they fail/not work when it really looks like they should. I might just make a guide including all necessary information for their replication.
Any questions/comments are welcome.