Quote
WARNING: You should not attempt to construct a pressure vessel of any kind from any of the materials listed unless you understand the requirements and risks of the pressure load you are applying and understand how to calculate the required thicknesses for a given material at a given pressure.
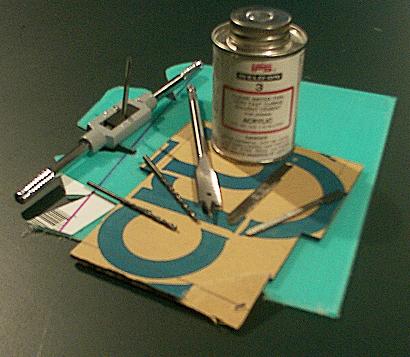
I'm hoping that this short will help alleviate some of the initial difficulties I have faced while working with plastics. I was fortunate enough to experiment with only scrap, but I've heard from a number of people who managed to destroy sheets that they paid good money for. These are the most frequently asked questions I see on a variety of forums and I will answer them as best I can. If you have any specific or complicated questions that I cannot answer directly, I recommend contacting a local plastics shop.
Materials
ABS (Pure, not ABS/PVC blend)
Desciption: Tough and impact-resistant, this material works well for protective applications such as small appliance housings. Commonly used to make hard-sided luggage and is the standard material choice for plastic injection molding (and therefore) it's what most plastic products are made with. Is 98% recyclable. Areas stressed beyond the point of elasticity will discolor before splitting.
Your average Nerf gun body shell is made from this material.
Highest operating temperature: 100+ F to 200+ F
Tooling behavior: Heats and melts very quickly above 125F. Use Slowest speeds possible with medium tooth count. Easy to carve with standard hand tools. It's a very soft plastic and can be difficult to machine predictably.
Avoid: Abrasive cutting tools or anything that creates excessive friction. Will fume excessively if heated so wear a filtration mask when cutting.
Commonly Available Colors: Black, Brown, Beige
PVC & CPVC
Description: A material you're all very familiar with due to it's low cost and ease of availability. Extremely high chemical and moisture resistance and very good impact resistance. However it mars fairly easily under abrasion and is relatively soft.
Highest operating temperature: 100+ F to 200+ F (300F for CPVC)
Tooling behavior: Provided the right blades are used, PVC can be as easy to work with as medium density natural woods. Behaves similarly to polycarbonate, but can be much more aromatic (smelly) due to its lower maximum operating temperatures.
Commonly Available Colors: Grey, White, Clear (expensive)
Nylon
Description: Good tensile strength and relatively low cost. Has a waxy feel much like polyester, but has a much higher temperature tolerance. Smells very much like paraffin wax when heated.
Tooling behavior: Is fairly easy to machine as long as the bits used when cutting or drilling are sharp and the part is kept relatively close to room temperature. Make sure to securely fixture into a vice or chuck when drilling holes larger than 1/4".
Commonly Available Colors: Black or Off-White
Polyethylene
Description: Coming in a very wide variety of material densities this plastic is the most commonly used plastic in product manufacturing due its low cost and ease of injection molding as well as recycling properties. Resists abrasion very well but has sub-par ability when it comes to structural rigidity and is relatively flexible, especially in lower density mixes.
Highest operating temperature: 100+ F to 200+ F (300F for CPVC)
Tooling behavior: Usually not desirable because it can become dimensionally unstable at lower temperatures, and melts excessively when being cut.
Polycarbonate
Description: Offers impact strength over a wide temperature range. Use indoors and outdoors. Offers a superior ability to resist being torn apart. They generally can withstand a pulling force greater than 10,000 psi. Has a greater ability to withstand a forceful sudden impact, similar to being struck by a hammer. Products listed with high impact strength generally can withstand 5 foot-pounds of energy per inch of thickness under normal conditions.

Highest operating temperature: 200+ F to 300+ F
Tooling Behavior: Shreds into fine pieces when the correct blades are used and it very receptive to tooling. Has a very low tendency to melt under friction, unless the wrong blade type is used when cutting it. Flexes easily and accepts high pressure amounts. Very easy to tap and drill. Machining experience comparable to aluminum in most circumstances.
Commonly Available colors: Clear, Opaque Black, White Tint, Grey Tint, Bronze Tint, Black Tint, UV resistant Black Tint (used for public transportation applications)
Polyester (PETG)
Highest operating temperature: 100+F to 150+F
Description: Extremely low cost Polycarbonate substitute material, but is considerably softer and therefore has lower abrasion resistance. Optical clarity is also lower.
Tooling Behavior: Can be temperamental in that it can cut a little bit too easily at times. Feels vaguely similar to wax and caution is needed to avoid overheating the sheets as they will become quite sticky against blades inducing friction. Generally pest to avoid this material if you need to cut out any complex or intricate shapes due to that property.
Polypropylene
Description: Most commonly used plastic across a wide variety of applications due to its low cost. It has a hard, smooth chemically resistant surface. Is non-toxic. Commonly used for pipes, valves, and fittings.
Highest operating temperature: 100+ F to 200+ F
Tooling Behavior: Heats and melts very quickly above 125F. Use Slowest speeds possible with medium tooth count. Easy to carve with standard hand tools but can discolor under pressure.
Avoid: Abrasive cutting tools or anything that creates excessive friction.
Commonly Available Colors: Black, Brown, White, Translucent White
Polystyrene
Description: A very soft and easy to cut plastic that is quite popular for kit-bashing due to it's acceptance of adhesives and paints. Also a very easy material to vacuum form with. Tensile strength is marginal and the material will snap when flexed too much. Is generally not a good material for applications that require dimensional stability or load bearing properties. Primarily only useful for cosmetic parts or limited use molds.
Tooling Behavior: Heats and melts very quickly above 200F. Use Slowest speeds possible with medium tooth count. Easy to carve with standard hand tools and can be cut with scissors provided the sheet is 1/16" in thickness or less.
Commonly Available Colors: White
Acetal (Delrin): An exemplary high density plastic that is and almost perfect aluminum substitute. Dimensionally stable, high tensile strength, wear resistant, and fairly impact resistant. Comonly used to make bearings, pulleys, and wheels. Only downside is comparatively high cost (mainly due to high density).
Tooling Behavior: Shreds into fine pieces when the correct blades are used and it very receptive to tooling. Has a very low tendency to melt under friction, unless the wrong blade type is used when cutting it. Flexes easily and accepts high pressure amounts. Very easy to tap and drill. Machining experience comparable to aluminum in most circumstances.
Commonly Available colors: Opaque Black and White
Acrylic (Cast)
Description: Moderate tensile strength material with good abrasion resistance qualities. Has low impact resistance and a tendency to split or crack under sheering forces. Optimal material in applications that involve heat-warping.
Highest operating temperature: 150+ F to 250+ F
Tooling Behavior: Better friction tolerances than ABS or Polypropylene, but will melt fairly quickly under friction. Can be very picky about blade types and lower blade speeds will need to be used. Much be worked with in a similar manner to balsa wood due its semi-brittle nature.
Avoid: Abrasive cutting tools or anything that creates excessive friction. Will fume moderately when heated so wear a filtration mask when cutting.
Commonly Available Colors: Clear, Opaque (White, Grey, Black, Red, Yellow, Blue, Green), Solid Tints (White, Grey, Bronze, Red, Blue, Green, Yellow, Amber), Fluorescent/UV Tints (Amber, Red, Green, and Blue)
Acrylic (Extruded)
Description: Often used to replace glass, provides outstanding optical clarity even at greater thicknesses. Has a smooth surface for use as windows and signs, but is less impact resistant than polycarbonate. Higher potential for fume production and more brittle than cast acrylic. Difficult to machine and has an even higher tendency to split or crack under sheering forces than cast acrylic. Most often seen in the form of bars, rods, tubes, balls, and discs.
Highest operating temperature: 150+ F to 250+ F (Does melt faster than Cast Acrylic due to its higher molecular density)
Tooling Behavior: Better friction tolerances than ABS or Polypropylene, but will melt fairly quickly under friction. Can be very picky about blade types and lower blade speeds will need to be used. Much be worked with in a similar manner to balsa wood due its brittle nature. Extruded Acrylic is slightly more fragile than Cast Acrylic and is therefore harder to work with.
Avoid: Abrasive cutting tools or anything that creates excessive friction. Will fume moderately to excessively(depends on the brand) when heated so wear a filtration mask when cutting.
Commonly Available Colors: Clear
Recommended Tools
ScrollSaw: Ideal for detail work and causes MUCH less friction that other reciprocating blade tools. Could ideally be used for the majority of cutting work that doesn't involve precise 90-degree measurement cuts. CAN be used for interior plunge cutting if a 11/16th to 1/4 inch pilot hole is drilled into the material. The blade than be untensioned and fed through the pilot hole.
TableSaw: In order to work with plastics you will need to purchase and use an OSB/Plywood blade (200 teeth) to prevent from cracking/splitting your sheets, which can lead to shrapnel. Higher bite angles work better for most plastics.
BandSaw: Fairly good tool for cutting plastics without splitting, or cracking sheets. Can melt extruded acrylic very quicky if setup improperly. Also one of the easiest tools to control the resulting mess from because all of the shaving come directly out of the bottom. DO NOT buy a new bandsaw that's cheaper than $125. These have alot of moving parts, so unless you can find an industrial-grade bandsaw at an estate or garage sale it's best to buy a quality name brand unit. Cheaper models may be finicky however and this is a very difficult tool to properly calibrate and maintain. So if you have a limited budget and little experience it may be best to opt for a TableSaw instead.
Jigsaw: A fairly good substitute for a ScrollSaw, especially when used for interior/detail cutting or sheet trimming. Much more predictable and variable for plastic cutting than a rotary tool. Use metal smooth-cut (24tpi) blades for most cutting. For smaller cuts or low heat tolerance materials scroll-cut wood blades (10tpi upcut/downcut) are recommended.
DrillPress: Far more controllable and precise than a hand power drill. Will allow you to use spade bits for larger holes as well as help you control your downforce.
Drill Bit Set: for holes smaller than 1/4" any drill bit set seems to work fine. But for larger hole diameters a plastic specific set or a good variety of spade bits is essential. I prefer using spade bits over hole saws or larger drill bits if I'm working with plastics (except for ABS and polypropylene which get "gummy" when spade bits are used).
Low grit count rotary sanding bits: These are very useful for shaping and smoothing out plastic sheet edges with either a rotary tool or a drillpress.
Hack Saw (or miter saw): While not at all usable with acrylic a hacksaw works really well with ABS, polyethylene, and thinner sheets of polycarbonate. I don't use these very often so I'm not sure which tooth counts will work best, but wood blades seem to work just fine.
Rotary Tool: While you can most likely do without this tool entirely, it's perfect for smaller shaping and etching tasks. It's not very useful for cutting most plastics though. To avoid excessive melting or blade sticking it's best to use high-speed cutting bits. Abrasive bits will not work properly with most plastic materials.
Needle Files: A triangular needle file works best for flat surfaces and a round one is great for curves. Bot are used for cleaning the edges of sheet after initial cutting, and before sanding them to a finished edge.
X-acto knifes: These can be use to carve softer plastics or use the dull side to deburr cut edges of plastic sheets. A good variety of blade shapes and lengths is recommended.
Deburring Tool: This is a thick handles pen looking too with a curved swivel blade on the end. It's made solely for deburring the edges of cut holes and can make quick work of cleaning up rounded edges and drilled holes. They can be difficult to find because they are machining tools and not woodworking tools so don't expect to find these are Home Depot or Lowe's. Mcmaster.com or Sears are the best places to look.
Heat gun (30w minimum): USE THIS WITH LEATHER WORK GLOVES, PLIERS, AND A FILTER MASK. This tool is extremely useful and allows you to heat-warp Acrylic and lower thicknesses of Polycarbonate. Must be used outdoors since sheets can leech fumes and the tool itself can be a fire hazard. You have to be careful with it though, and refusing to wear protective gloves will lead to injury. Hot plastic gets tacky and will stick to skin or burn you really quickly. Nevermind that you're also working with a tool that operates above 350F. DO NOT USE GLOVES THAT ARE NOT LEATHER or otherwise unrated as fireproof.
Strip Heater: USE THIS WITH LEATHER WORK GLOVES, PLIERS, AND A FILTER MASK. For long straight heat-warping bends this is the ideal tool. It can heat a wide area evenly and at a more predictable temperature then a heat gun.
Sandpaper (250 to 1000 grit): If you want finished edges, this will be the most effective method. Flame polishing is a difficult method to perfect and will only work with acrylic so I don't recommend it unless you have a stockpile of scrap to practice on first. When sanding plastic you don't have to progress as slowly as you would when sanding metal, so you may only need 3 sheets (400g, 800g, and 1000g) to get glossy edges.
IPS Weld-on #3 or #4: This is an extremely useful and effective plastic solvent that fuses ABS, Polycarbonate, and Acrylic together (in any pure combination of the three). Simple brush onto or apply to contact area with syringe then secure pieces together in the final form you want. #3 formula is slightly thicker and faster setting, while #4 is water-thin and sets more securely. #4 is recommended for anything you are trying to make air-tight because it's thin enough to use capillary action to fill all of the gaps between the sheets you are joining together. In order to join sheet edges securely and tightly make sure they are sanded to atleast 400grit level and are straight enough to make a scure bond. You do not have to apply any contact pressure to get a good chemical bond. Over application will lead to ugly, but working joints. Can be applied an reapplied as needed without complications.
It's a good idea to use this in a ventilated area, and while it will not adhere your skin to plastic it WILL create permanent fingerprints. This is a mildly toxic substances so excessive skin contact is not a good idea.
It with also work with butyrates and styrenes, but I have not tested it on polypropylene or polyethylene yet so you'll need to ask a plastics shop about compatability. I do know that it is completely incompatible with all PVC plastic blends so avoid buying ABS/PVC (Kydex T). ABS/PVC is a crappy plastic anyways. If you need a specific solvent for a material, check out the wide range of products available from IPS: http://www.ipscorp.com
Both #3 and #4 (and a whole host of other plastic adhesives) are available from McMaster (page 3229).
To apply Weld-on accurately and safely I recommend using 3ml luer-lock syringes with flexible PTFE tubing "needles".
These can be purchased from medical supply, or through industrial supply catalogs such as McMaster (part #s 7510A651 & 75175A691)
Safety Glasses: For the most part plastic isn't dangerous to work with since the particulates create from cutting are low weight and low velocity so impact resistance is less of a concern. However, goggles are vital for protecting your eyes from dust and shavings while tooling or sanding. Regular safety glasses will work fine.
Water-jet cutting: Yeah, I wish I had access to this frequently too. Water-jet cutting will work just fine with all of the above listed plastics provided you don't make your design with too many small poorly supported pieces. Polycarbonate can withstand lots of stress while having some extremely small pieces left after cutting, but with ABS and Acrylic any pieces that are connected with joints thinner than 9/16 will probably snap off in the process of cutting.
Machining Plastics
Plastics are quite temperamental when it comes to machining. Only certain tools can cut them safely and reliably and you have to work at a pace of patience or you'll end up ruining your sheets. Or even worse, getting yourself injured. Out of all the available materials in this category, polycarbonate is by far the most forgiving. So if you have no previous experience working with plastic, or you have limited access to tools, it would be a good idea to consider using only polycarbonate in your project.
Before working with plastic you also have to take into account blade speed, friction, bite angle, tooth-counts, fume production, and pressure. For tool recommendations see above, but the general rule of thumb is work slow, and work with as little force as possible. Especially if you're working with brittle plastics.
When Cutting: Feed slowly, avoid friction, avoid side-forces, use the right blade. Slow down or stop if melting starts. Allowing melting to continue may eventually allow the blade to yank your work out of your hands, or it could simply ruin your power tool. Plus, metling also leads to fumes, and those can give you the nastiest headaches you've ever experienced in your life.
When Drilling: Use slow to medium speed and only slight downward pressure. Optimally the drilling process should sound like waves on a beach or sandpaper rubbed on metal. Make sure to clean your drillbit off after drilling each hole (the heat gun is also extremely useful for this). For drilling holes 1/4-inch or larger use spade bits or bits made specifically for plastics. Plastic specific drill bits have a shallow bite angle to prevent the drill bit from digging into the plastic and therefore getting stuck and biting a piece of your sheet off in the process. If you're going to be working with plastic quite frequently, a plastic specific drill bit set will save you alot of time and frustration.
When Sanding: Plastic is as easy to sand (or more-so) as more soft crafting woods like balsa. Lower heat tolerance plastic melt wuickly though, so if you use power sanding tools (again) low speeds will be the most effective. When sanding with power tools the powder that comes off is heavy, but can stick to everything and get everywhere so you will need to wear a filter mask and goggles. Manual sanding isn't as messy so unless you sneeze a filter mask and goggles won't be required. I found that the more brittle the plastic, the more likely it is to produce razor-sharp edges when filed or sanded at angles. So if you are jointing pieces at corners or mitring sheets it's a good idea to wear gloves when sanding such pieces.
When Tapping: Excluding Acrylic, drilled holes in plastics are very very easy to thread with even the cheapest tapping set. Here are the drill bit sizes you need to drill pass-through holes for mounting and holes to tap for the standard screw sizes.
M3 (Machine screw used primarily for optical drives)
Pass-through: 1/8-inch
Tap: 3/32"
#6 gauge 32 thread count (UNC #6-32 Common case screw)
Pass-through: 9/64-inch for closest tolerance or 5/32-inch
Tap: 7/64-inch
Acrylic can be difficult to tap, especially extruded. Shallow threaded holes are fairly easy, but anything deaper than 1/4" becomes difficult. You have to go slow and if its start resisting, forcing it will lead to fractures or splitting. With acrylic it may help slightly to use a heat gun while tapping a hole.
The rest of the plastics listed above however are very easy to tap and shread easily making way for the tapping head.
Raw Plastic Material Shopping Sources
1. CHECK YOUR LOCAL PHONE BOOK. Plastics shops and signmaking shops 9-times-out-of-10 will be selling their scrap plastic for a few dollars per pound. For some materials and tints you can buy whatever you need for 75% to 90% off warehouse or industrial pricing. Obscure items will obviously be hard to come by but you can save alot of money if you just look locally first.
2. http://www.mcmaster.com
3. http://www.usplastics.com
4. http://www.tapplastics.com
5. Many other online stores. I haven't checked other regions but I can try to find them if anyone asks.
Making precise machining templates
(with a cheap inkjet printer.)
One of the more irritating hurdles to making your plan become a reality involves converting your plan to actual dimensions to work from on your raw materials. I used to do this markup process using a mechanical pencil and a schematic to work from. This took alot of time and only produced precise results part of the time (due to scribing errors). Machinists use scribing all the time, but they have far more accurate measuring tools than I have at my disposal.
After a recent project I realized I could use my printed to eliminate the need for scribing measurements on my part. This method is meant for any part that is 10" x 8" or smaller. Anything larger and you will have to combine sheets or find a local print shop that can print much larger labels or decals.
Software
There are so many options for software, and most of the more common titles cost more than the average person can afford. I've tried every free trial there is available and I've found one to be the easiest to learn and the most useful since it's an unlimited free trial.
Alibre Xpress is the free version of the full package and will allow you to design simple assemblies and part templates for whatever use you want. It's configured similarly to other Solid CAD programs in that you simply make a sketch on a plane then use one of several methods to extrude the sketch into a solid shape.
Step One: Measure & Sketch
Obviously if you're going to make a part you need measurements to work from. Whatever part you're making Alibre will allow you to sketch in the details you want. For hole placements relative to a corner simply start a line from the center (x0y0z0) by clicking there and then right click and select "Direct Coordinate Entry" which will allow you to place the other end of the line relative to the start of it.
Just continue sketching until you have a finished part.
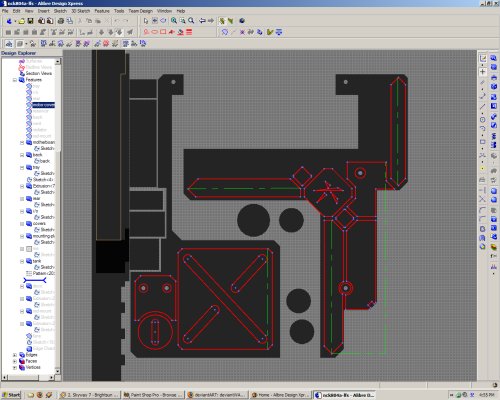
Step Two: PrntScrn
Screen capture the sketch from Alibre with the sketching grid turned off. In a graphics program paste the screen shot and crop the image around the sketch. Select only the sketch lines and sketch nodes and copy then paste into a new image. Use brightness/contrast to turn the sketch black and then flatten the image.
Step Three: Page layout & Printing
Save as a temporary image and load as Clip Art from File (or just paste) in Microsoft Word (or similar suite). Right click the image and select properties to change the image dimensions to match the dimensions of the sketch in Alibre.
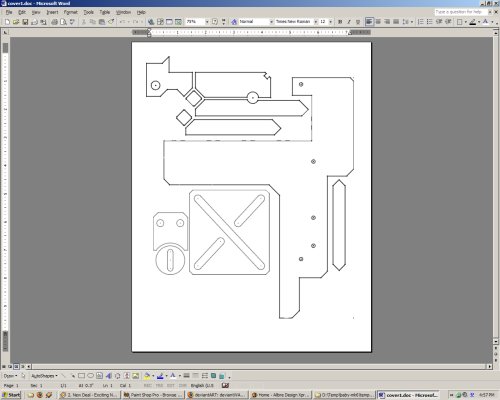
For smaller parts you can fit multiple sketches on a single page. It may also help to save your sketch images as .PNG files with an Alpha Channel layer. That image type seems to scale more cleanly in Microsoft Word for some reason.
Put one full-sheet label in the printer face down and then print your template page at the "Best" quality setting in your printing options so that you are printing at a quality level of atleast 600dpi. A lower DPI will result in extremely pixelated and difficult to use templates.
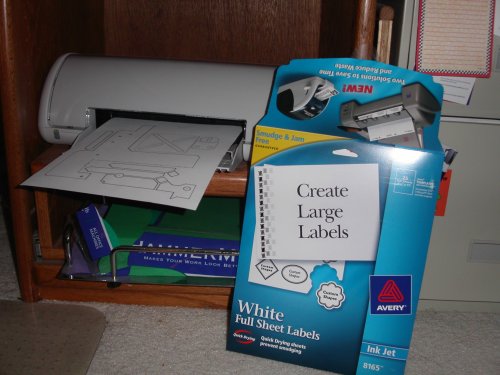
Step Four: Application
Now simply use some sharp scissors to cut out your individual cutting template labels and apply them to your sheets. It's best to apply them onto the protective film that comes on the sheet because cleaning the label adhesive off of the sheet after doing all of your cutting and drilling can be a time-consuming process.
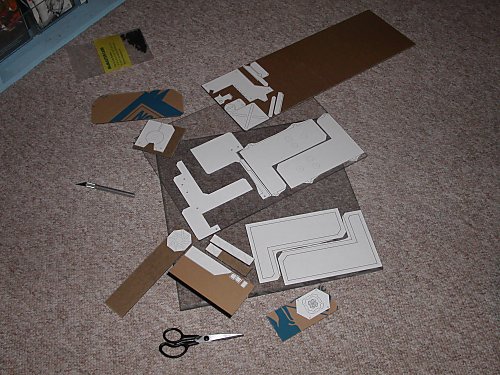
Step Five: Assembly
Now that all of your individual parts are cut and drilled you can put them together as planned using whatever method you intended.
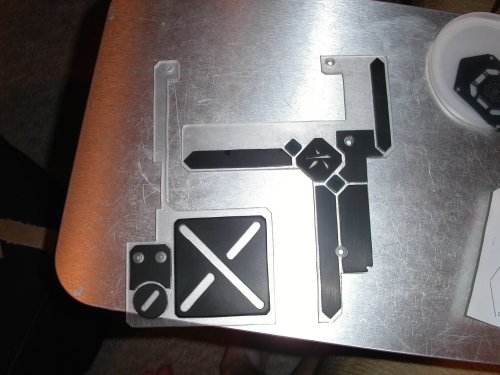
That covers most of what I've seen asked several dozen times. If there's anything you'd like to see added or questions you have feel free to contribute.
Edited by CaptainSlug, 28 May 2009 - 12:45 PM.