Alright, so this Is something I have been working for a few weeks, but haven't mentioned. I was gonna keep it secret untill i finished, but hey, this could really help someone in the homemade contest. This is a simple working concept that I am in love with. I have looked and found nothing like it, but it may have done before. It will be a while before I finish it, but I thought I might share it with someone so they may have one of those OMG THAT'S IT! moments.
Diclaimer:
Wile this is a concept, I have done some work with it, and will upload more pictures shortly. Some of the the stuff I put in the diagrams are not homemade. I put them there because it makes it easier to understand. Yes, i realize there are some things, but more detailed diagrams will be posted as soon as I can. Yes, I realize this is a concept right now, but I will post more really soon, as I am having technical difficulties, so please don't ban me.
So let's begin. What is the hardest part of a homemade, especially clip fed ones. The damn feeding system. Anyone can make a semi auto valve system, but making a breech that will go forward, fire, then back up is just a pain in the ass. And rate of fire is limited also by the fact that the dart can only enter the breech for a fraction of the full cycle. So I've been looking into alternate breech methods, and I finally got one
A rolling breech. Imagine an angle breech, but instead of a back and forth motion, it spins. Two telescoping pieces of brass each with a breech cut in it. The inner one is Spun by a motor. When the brass lines up, the dart slides in, when they are opposite, it seals. Combine that with an electrically operated switch at the bottom that triggers a semi auto valve, and you have a auto clip fed rifle. More info comming really soon
Here are some of my pretty pictures/diagrams
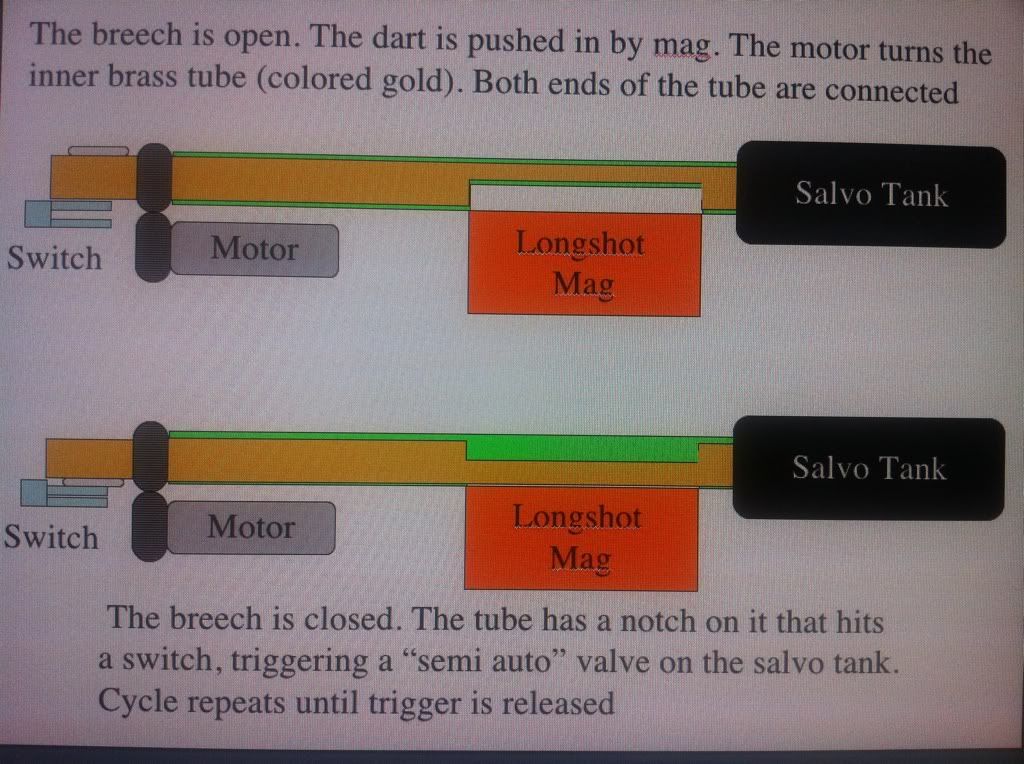
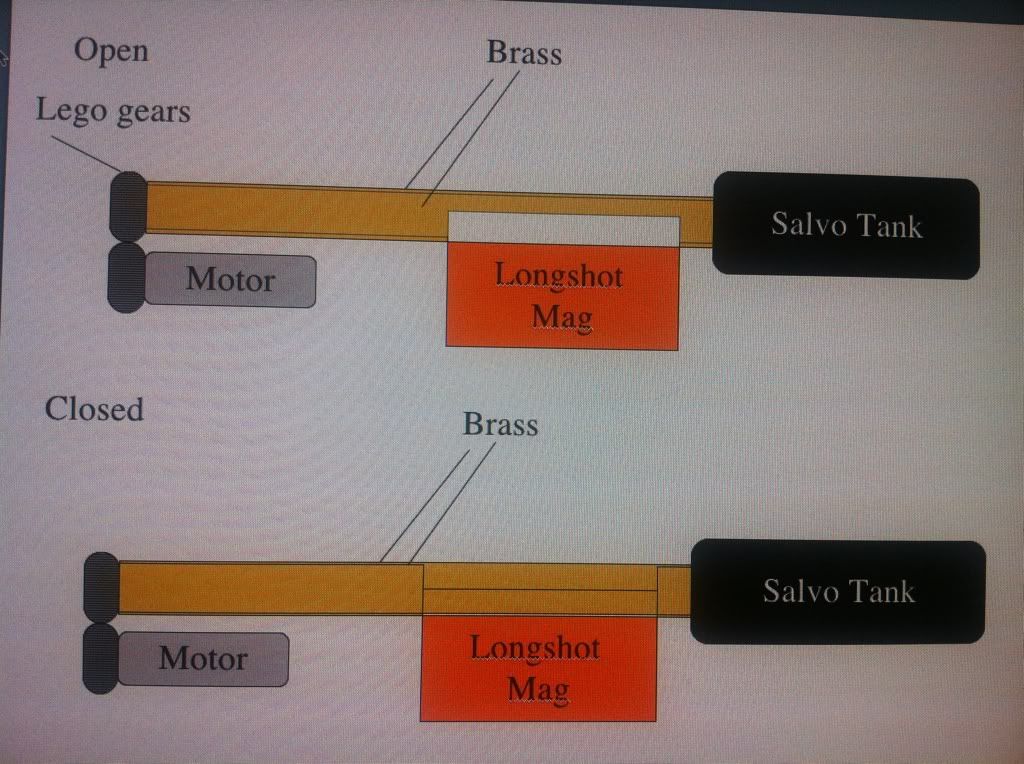
Hope you like

Here is a simple mockup of the breech. All my stores are out of brass, so I made it using spare parts.
Closed

Half open
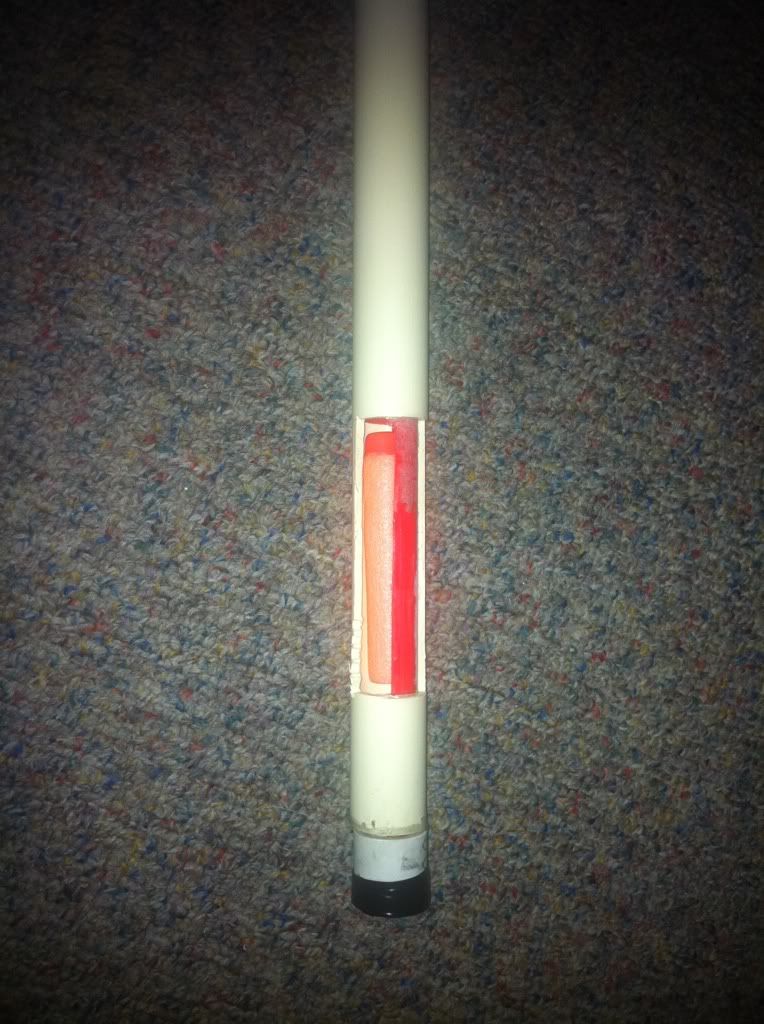
Closed
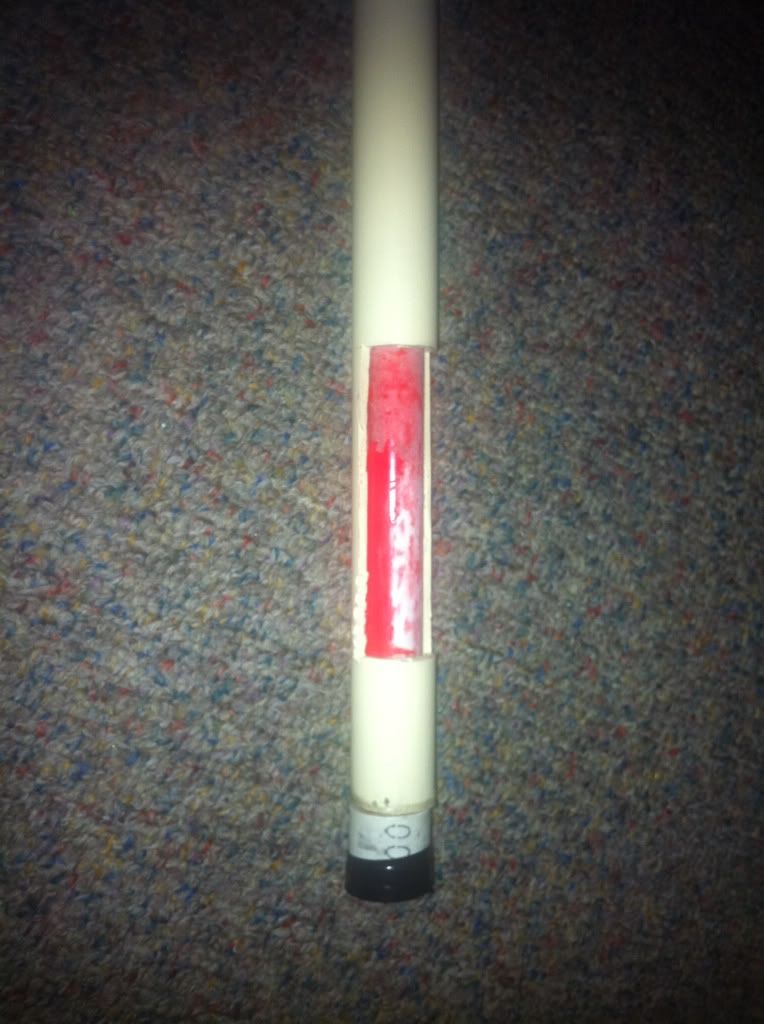
Edited by Dyxlesic, 24 May 2011 - 07:36 PM.