SGN-PAR55M - Pump Action SystemThe system starts with a basic plunger head build.
In my example i simply cut a circle out of a thick rubber sheet to match the 55mm ID of the plunger tube (i had to do a few test fitments with some trial & error to get the ideal circle dimensions), then sandwiched the rubber circle within 2 pieces of plastic discs (any other suitable disc shaped materials can also be used).
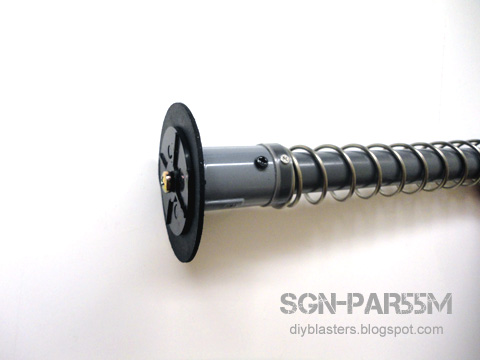
Its best to use rubber material which is thick and rigid enough not to fold when under pressure, this ensures there is no air leakage during usage.
The plunger head is bolted securely onto the plunger rod and end cap with a large screw.
Yes... i know, many expert blaster builders will bemoan my use of such a rudimentary plunger head setup, it definitely isn't as sophisticated as the skirt seal plunger heads seen on other blaster designs. It was actually intended to be just a quick setup for testing purposes, but surprisingly it could still achieve 100% air seal and optimal performance with this simple plunger head configuration, so i decided to just stick with it for simplicity (watch the demo video below to check out the air seal performance).

To create the pump action system, i cut guide slots into a length of 20mm PVC pipe at the shoulder stock section. I used a Dremel with a cutting bit for wood/pvc (metal disc with serrated edges) to cut the slots.
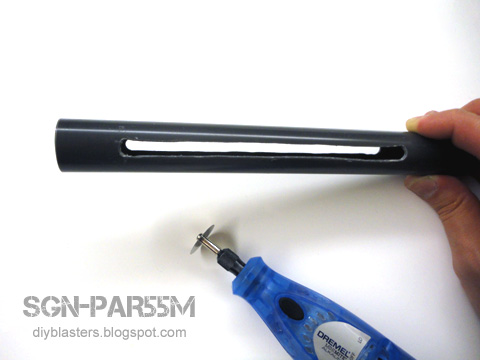
The slot length is around 15cm (approx. 6") to match my intended plunger draw. The slot height is around 5mm, to accommodate the bolt that will be used for the priming bar.
A pair of matching slots is also cut into the 13mm PVC plunger rod to facilitate the linkages within the pump action system.
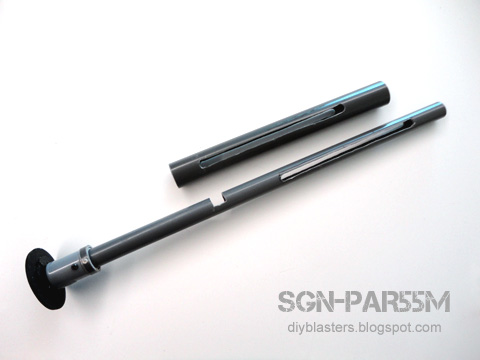
The measurements on the cut-out slots have to be accurate and aligned correctly. Just take your time and measure everything properly beforehand. With abit of steady cutting and patience, its quite a straightforward task to accomplish.
Next step...
Remember the modular
PVC Pipe Catch Ring & Trigger component from the
SGN-R3L? If you have already built a set, then most of your work is already done! Simply take your existing catch & trigger component and just connect it up to the shoulder stock design of your choice.
The advantage of these modular components is that you can just swap them around or replace them easily.
If you've not built your modular PVC pipe catch & trigger component yet, then just refer to the
SGN-R3L overview to see how its made.
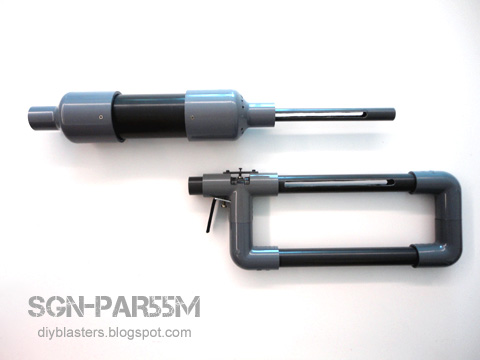
Assemble the plunger tube. I use a section of 55mm ID PVC pipe with matching front and rear pipe reducers. The plunger rod and spring are positioned inside the plunger tube.
The pipe reducers are secured with counter-sunk machine screws, this is so that the pump grip can slide over the reducers without getting blocked by any protruding screw heads.
Notice also in the above photo... other than the catch, trigger and reducer sections, there are no machine screws securing the rest of the pipes and joints?
I discovered that with this design, most of the pipe parts are connected in a set and are not load bearing sections, so the entire blaster can work perfectly even when those sections are not bolted together. This also helps to facilitate easier and quicker swapping of parts.
To assemble it, simply pull the trigger (to open the catch), then connect the plunger tube/rod section and the catch/trigger/shoulder stock section together. Note how the plunger rod slots are aligned with the shoulder stock slots.
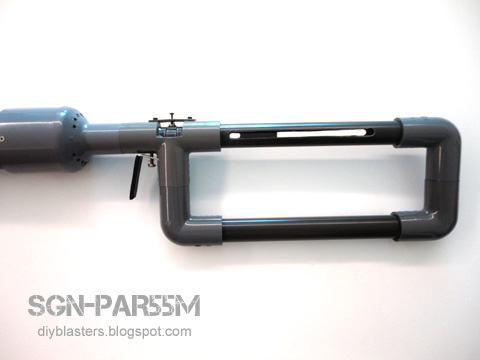
With this modular assembly method, both the front and rear section can also be easily detached by just pulling them apart for maintainence or transportation, no tools required.

The large plunger volume will generate alot more vacuum draw behind the plunger head when it propels forward during firing, so make sure there are enough air relief holes drilled into the rear reducer to offset the vacuum draw (if air relief holes are not done or insufficient, the vacuum draw will slow down or even stop the plunger from moving forward).
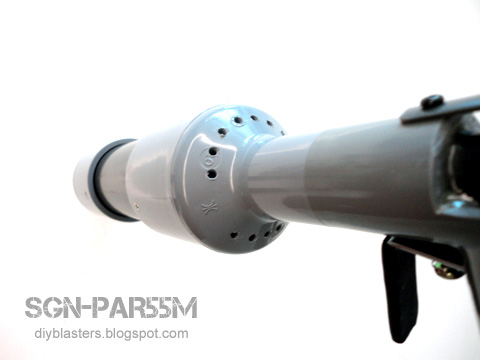
Next, we'll now proceed on to the pump grip.
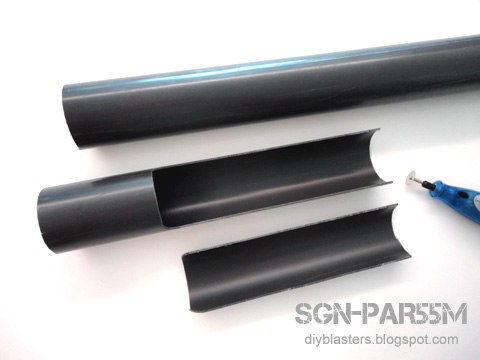
In my example, i used a section of 70mm ID PVC pipe, this particular pipe size fits smoothly over the front & rear reducers i used, therefore perfect for use as the pump grip.
Do a test fit and match the grip length required, then cut out the shape (length will depend on the overall dimensions of your particular pipes and joints).
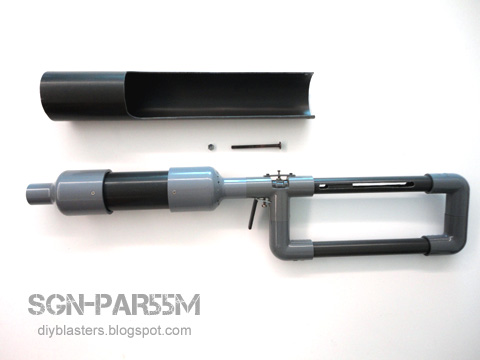
The pump grip is sleeved over the reducers and secured to the plunger rod via a long carriage bolt and nut threaded though the shoulder stock and plunger rod slots.
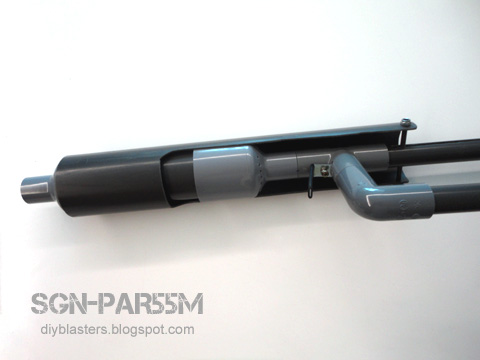
The grip section can be easily detached anytime by simply unscrewing the bolt.
Make sure the pump grip is able to move smoothly back and forth. Some additional trimming on the slots or parts in contact may be required to fine tune the fitment.

Its done!
The pump action grip also acts as a kind of blaster casing cover for the PAR55M, giving it a sort of "carapace" shell casing. Makes the design look abit more cohesive.
Edited by SgNerf, 29 April 2011 - 12:54 PM.