How-To: Porting
Part One: "Properties of a Cylinder"
Well, a long time ago, in a galaxy not far, far away, a very artistic member of NH ranted about hole patterns (or lack there of) in homemade silencers (was it NinjZ?). Hopefully that will never happen again. There are a lot of pictures here, most taken in shit lighting, so stick with me...
This guide is to prevent one of these. Sorry about the owner of that pic, who I will keep anonymous, for using it in such a way...
First off, what you will need (to make your life easier):
- A drill press
- Drills
- Masking tape
- A ruled straight edge
- Scissors/Paper Cutter
- A writing tool
- A piece of unlined paper
- A very sharp, very fine bladed knife (i.e. Xacto knife with #11 blade)
- A center punch
- Something round to turn into Swiss cheese
- Sandpaper
1.) Start with the piece of paper. Wrap it around the pipe like so:
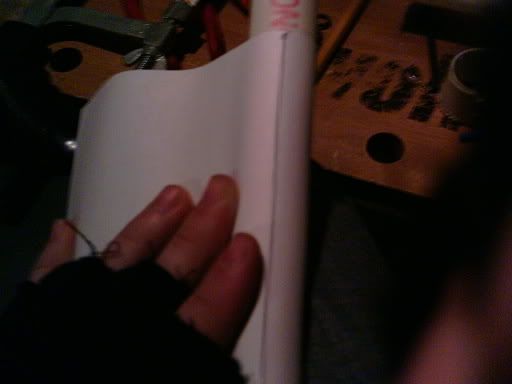
Then mark where it overlaps, like in that previous picture. That piece of office-size paper is a bit small for the length used; however, this is going to be a 12" total-length silencer made of 3/4" decade-plus-old Sch40 pipe. The pipe (cut, squared, trued, lapped, sanded slightly) is here:
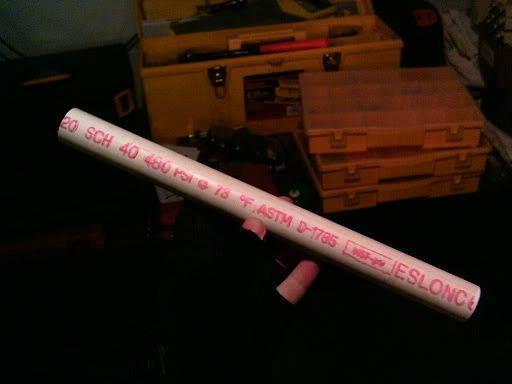
2.) Now that you have that done, remove the paper and grab your indexed straight edge. Use either millimeters or inches; I prefer inches since that is on the outside of my 8-sided architectual-ruled straightedge. Measure the length you have to work with, as in, what would be the circumference of the cylinder net (width of the rectangle) you just made:
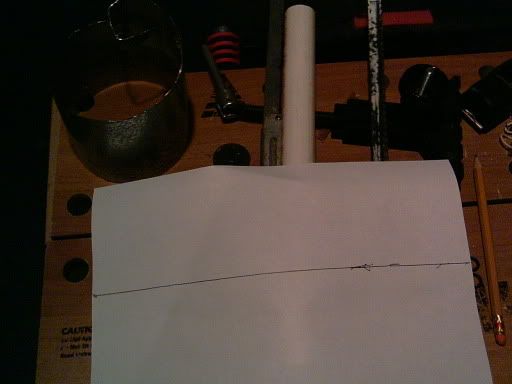
Now take that measurement, and divide by a whole number until you get a fraction/decimal which can be used for your scale. Try and make the number of holes fit with the piece; If you are making a silencer, four holes per row would be "t3h Sh!t5" since there is not enough total surface area to give any good flow. Remember to keep in mind the size of the drill you are working with; a .25" drill will not be good for a small pipe like 1/2" CPVC, unless that truly is what you need if for (two holes on opposite sides?). Write the spacing (circumference divided by number of holes) and write it down someplace. That will be needed later.
3.) Find out how much space between rows you want. I usually use twice the diameter of the drill.
Draw lines which go parallel to where the base of the cylinder net would be, like so:
(picture coming soon)
4.)Then take that number you wrote down, and start measuring off each tic starting from the first circumferenctial line. The number of holes should be the number of tics. See here:
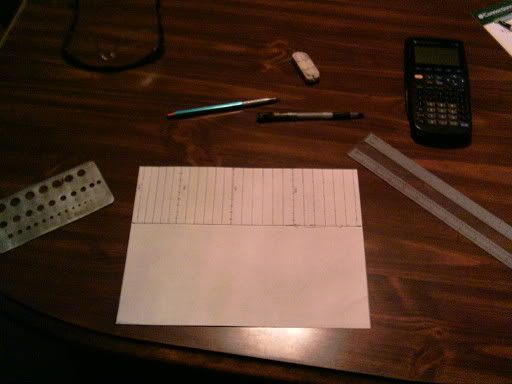
5-a.) Now, for straight lined holes, like this:
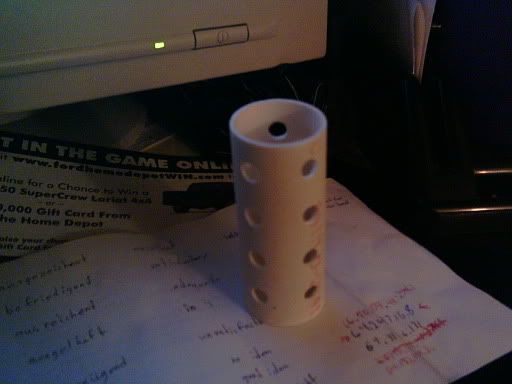
(secondary baffle for a silencer)
You simply start each row of holes at the same place. Otherwise, for spiral porting (5-b.):
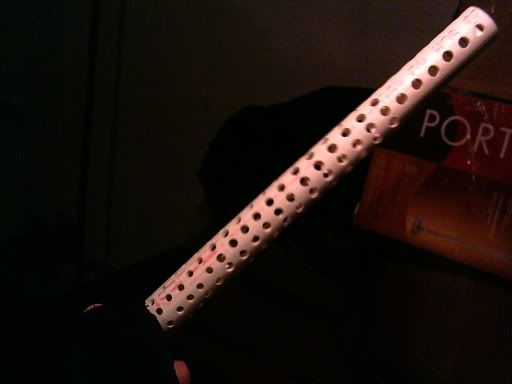
(a large suppressor core)
Or staggered porting (5-c.):
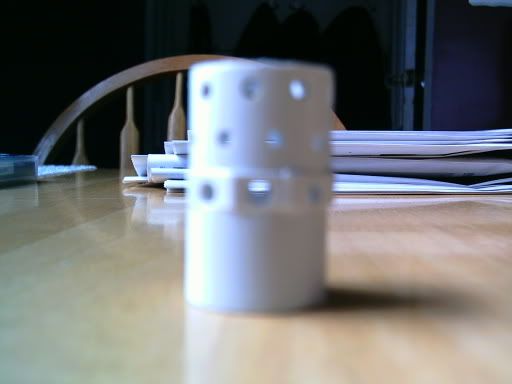
(muzzle brake)
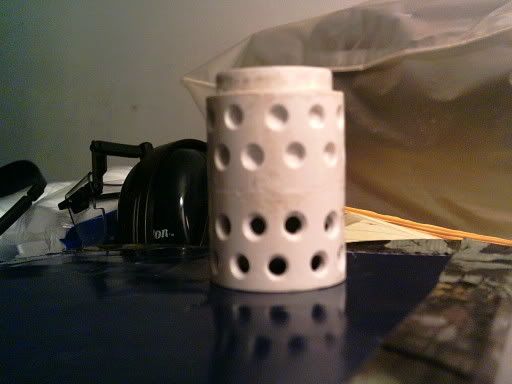
(piston for BSC-LR)
5-b.) Take that half and divide it again, starting the first row at zero, second at 1/4, third at 1/2, fourth at 3/4, and fifth at zero, etc. Then you get something similar to this:
(picture coming soon)
5-c.) Take the space between each hole and divide it in half (staggered) to start every other row:
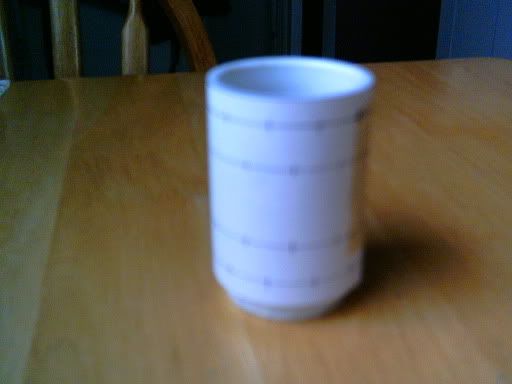
Now, if you are just porting something for an interesting muzzle brake:
(picture coming soon)
Only use half the circumference or 3/4th or whatever and go back to step 2.
Also note that step 5-B is just an example. My silencer did not use that; every hole in a row was spaced 3/8" so I made the stagger 3/8" across 6 rows, or each row was 1/16" offset -clockwise- from the previous.
6.) Center punch each cross. Drill at the center punch indentation. Remember feed and speed rates. I was running as slow as my drill press could go (720 RPM), but should've been having the bit turn slower (400 RPM).
(need to redo video)
7.) Clean up the whole pipe, both inside and out. Use that ka-nife I listed earlier.
(need to redo video)
8.) Sand down the outside of the pipe because I told you to. Also sand the inside if it is short.
9.) Install and Enjoy! Alternatively, use 3" pipe to make a ceiling fan light cover you broke while yanking too hard on the pull switch!
(pictures coming soon)
I will probably make this go a bit smoother by removing some of the vocabulary and whatnot, but that is for a later edit. I also need to make a muzzle brake for a friend's SuperSoaker, which I will take the remaining pictures for and edit them in here. Also, I will take new video and post it. I kinda messed up due to lighting and whatnot. That and I'm too lazy to install the software to edit it...
Edit: I think this was my 400th post...wow...
Edit2: Added pics, fixed some grammer/spelling errors...
Edited by GeneralPrimevil, 08 April 2006 - 09:50 AM.