A few years back, I started a hobby project centered around Nerf custom gunsmithing. Essentially, I want to design Nerf-compatible weapons that look production final, and perhaps offer them up on limited casting/painting runs.
I went on hiatus due to jobs and moving... but now things are settled down, and I can return my attention to it.
The first project is called XB-REV-001, and is a "reskin" of a Maverick. It is designed to cannibalize the internals of a Maverick into a new shell.
I am hoping to create a series of weapon reskins that carry my own design aesthetic, yet remain compatible with Nerf darts and accessories.
The process goes a little like this (and I'm still figuring some of this out as I go):
- Concept sketches
- 3D mock-up in Sketchup
- Engineering to accomodate internals
- 3D print shell for scale and adjustments (Shapeways)
- Detail sculpt in ZBrush
- 3D print prototype parts
- Mold and cast final weapons in high-quality epoxy resin
Here, i will be tracking the development of the XB-REV-001. I'll try to keep all the progress in this first post, and just compact old information (and collapse images into links.) So... here we go...
CONCEPT
The XB-REV-001 is intended to be an eXperimental Blaster, built on the REVolver layout of the Maverick, first in its series.
I wanted to design something that was a low-axis barrel revolver configuration (like a Mateba or Rhino) and compact in comparison to most Nerf blasters. As a base model, I wanted something snub-nose, but I have ideas for longer and tactical versions (with more integrated rails under the cylinder.
Here is the sketch:

3D MOCK-UP & ENGINEERING
One of the biggest challenges in converting the Maverick internals into a low-axis revolver was figuring out how to get the trigger mechanism connected to the cycling mechanism. The plastic arm that would extend up and around the piston was getting so long that I started thinking it would just turn into a flexible lever.
Instead, I came up with the idea of linking the piston cocking mechanism to the cycler, and modifying it to lock into position when the slide returns forward. This means the cycling mechanism will have a recast part, and no longer will the cylinder rotate into firing position during the trigger pull.
The trigger now makes a firmer mechanical connection to the piston release rather than interfacing through a lever. Everything else works as expected.
The cylinder itself will be locked into the frame, and, as you can see, the top 3 chambers are exposed, so you can reload whenever without having to pop the cylinder out.
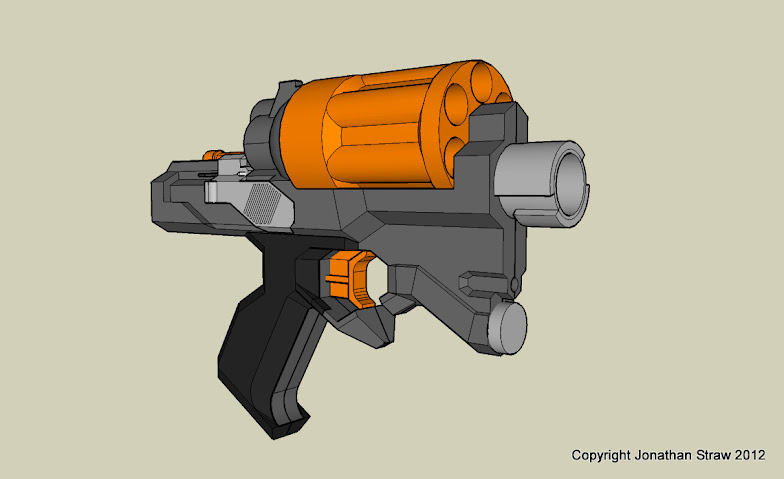

With internals visible:

And finally, the barrel is based on the Nerf standard for adapting barrel extensions, as shown here with the Recon barrel for demonstration purposes:
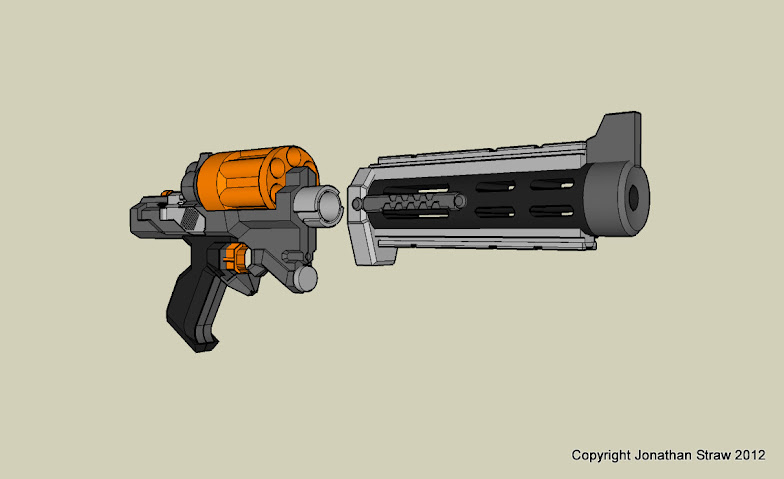
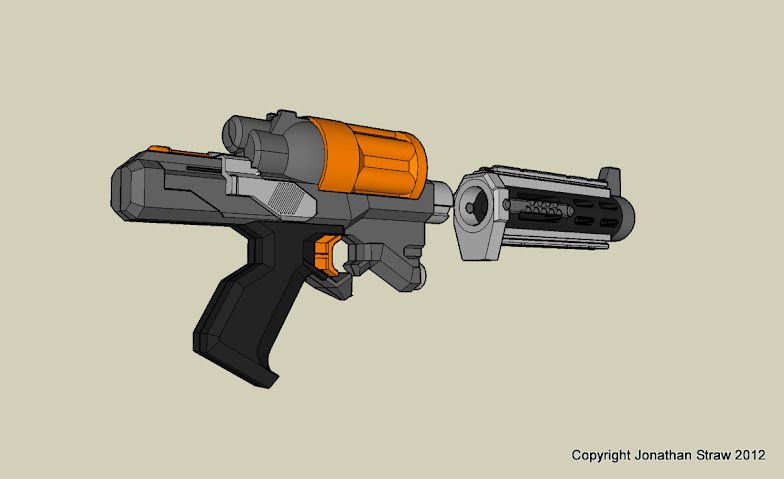
Next up... I have to work out the internal void of the shell, mount points, and guides inside the weapon.
...Comments, suggestions... always welcome. I'm making this for you!