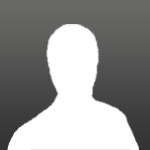
Motor-primed Springer help
#1
Posted 17 May 2018 - 11:39 AM
I did some measurements. Priming the Disruptor requires pulling back 6cm, for a peak force between 4.6 and 5.2 kg (let's assume 5).
So the question is, what kind of motor specs would I need to pull 6cm against 5kg of force in about half to one second?
#2
Posted 17 May 2018 - 02:24 PM
If you could somehow make this work with a dartzone magnum super drum.......
40 rounds full auto from a front loading revolver with 70+ FPS. And magnums are still in stores, and are still 15 dollars. HOLY SHIT
imma go fuck around with a dartzone magnum now.
Adios
#3
Posted 17 May 2018 - 07:04 PM
The question is on the motors themselves. What wattage do I need? What other specs? What does it take for a mottor to lift 5 kg across 6cm in 0.5 seconds?
#4
Posted 17 May 2018 - 07:07 PM
#5
Posted 29 May 2018 - 12:04 PM
#6
Posted 29 May 2018 - 12:55 PM
Well, I'm... kind of looking for the minimum sufficient. I could put it up on a car engine if I wanted to, and it would work (or get crushed), but I'm more looking for the line between 'works' and 'doesn't' so I can see what works and what doesn't.
#7
Posted 31 May 2018 - 08:11 AM
Use 180s
#8
Posted 31 May 2018 - 08:30 AM
Yea, but that... doesn't answer the question.
#9
Posted 04 June 2018 - 08:29 AM
POPULAR
Not sure how much information/background you have/need, so I'll just infodump and we can weed through stuff together, I suppose.
Now, I assume that you're using a motor to push a gear, bit like an XSW kit, and leaving the thing on slamfire.
So for the following equations, assume that length refers to the pitch diameter of the sector gear that the motor is driving.
Calculating the amount of torque the motor needs:
http://hyperphysics....base/torq2.html
This should give a quick overview of translating torque to force and vice versa.
TL;DR - torque = length x force
Translating RPM and omega:
Here's how to translate RPM to rad/s, because that's more useful for our calcs.
https://sciencing.co...ns-8343758.html
Here's a calculator if you're lazy
https://www.convertu...o/radian/second
Translating omega and velocity:
tangential velocity = omega x length
So that's basically how to calculate required operating RPM and torque. Now, you don't actually have to get a motor that fits this - you can use a gearbox, which messes with the torque and rpm outputs, via mechanical advantage, but I'm guessing you already thought of that. Hope this is useful, feel free to ask for more/less detail, I'm more just dumping this info so we have a starting point for discussion.
Alternatively you could just get a swarmfire or speedswarm, but hey, R&D is always cool to see.
#10
Posted 04 June 2018 - 03:02 PM
Not sure how much information/background you have/need, so I'll just infodump and we can weed through stuff together, I suppose.
Now, I assume that you're using a motor to push a gear, bit like an XSW kit, and leaving the thing on slamfire.
So for the following equations, assume that length refers to the pitch diameter of the sector gear that the motor is driving.
Calculating the amount of torque the motor needs:
http://hyperphysics....base/torq2.html
This should give a quick overview of translating torque to force and vice versa.
TL;DR - torque = length x force
Translating RPM and omega:
Here's how to translate RPM to rad/s, because that's more useful for our calcs.
https://sciencing.co...ns-8343758.html
Here's a calculator if you're lazy
https://www.convertu...o/radian/second
Translating omega and velocity:
tangential velocity = omega x length
So that's basically how to calculate required operating RPM and torque. Now, you don't actually have to get a motor that fits this - you can use a gearbox, which messes with the torque and rpm outputs, via mechanical advantage, but I'm guessing you already thought of that. Hope this is useful, feel free to ask for more/less detail, I'm more just dumping this info so we have a starting point for discussion.
Alternatively you could just get a swarmfire or speedswarm, but hey, R&D is always cool to see.
Now we're talking! Our torque will need to be 0.06 X 5 or 0.3 newton meters (am I doing this right?)
And for a simple 1-2 shots/second, we need a tangential velocity of 0.06-0.12 m/sec. But what's the omega, and what length are we referring to?
Then we'll have the minimum torque and rpm (or with a gearbox, their minimum product) and anything over that does it. Right?
Sure, i could go straight for the reasonable approach of getting a blaster that does what I'm trying to do, but I guess I'm kinda in love with the disruptor's feel. Might be just that it's my first nerf
#11
Posted 05 June 2018 - 12:23 AM
Now we're talking! Our torque will need to be 0.06 X 5 or 0.3 newton meters (am I doing this right?)
And for a simple 1-2 shots/second, we need a tangential velocity of 0.06-0.12 m/sec. But what's the omega, and what length are we referring to?
Then we'll have the minimum torque and rpm (or with a gearbox, their minimum product) and anything over that does it. Right?
Sure, i could go straight for the reasonable approach of getting a blaster that does what I'm trying to do, but I guess I'm kinda in love with the disruptor's feel. Might be just that it's my first nerf
Yep! I did say diameter, but I should've said radius. And come to think of it, length is probably the wrong term for me to use, I should really use radius instead.
So sort of like you said, with a gear of radius 0.06m, and a force of 5N, you would result in a torque of 0.03Nm.
Just to check that we have an intuitive understanding, imagine you have a 1m arm outstretched, and you're holding an item that weighs 5N (so like 0.51kg or so), your muscles would have to generate 1m x 5N = 5Nm of torque to hold the object up. Similarly, with a gear of say, 6cm (or 0.06m) radius, with a force of 5kg (or 49N), we'd need a torque of 49N x 0.06m = 2.94Nm. Usually when speccing motors, people seem to like using kgcm for some weird reason (yuck, using kg as a unit of force), so it'd probably be more appropriate to describe the torque as 5kg x 6cm = 30kgcm. Note that this is the same value as 2.94Nm, just in different units.
TL;DR - (tangential force on spinning thing) x (radius of spinning thing) = (torque of spinning thing)
Now with omega, omega is basically rotation speed in a purer form, since we're using radians instead of rotations, or degrees. Once again, I should've said radius, not length. So like with a wheel, or a gear, if it's rotating at say, 2 radians/second, and it has a radius of 5m, then the surface velocity (the velocity on the surface of the wheel) of that wheel or gear would be 10m/s.
TL;DR - (omega of spinning thing) x (radius of spinning thing) = (surface velocity of spinning thing)
With the motor selection, yep, ideally you'd pick a motor/gearbox combination with an "nominal torque" and "nominal RPM" that's higher than both your required torque and RPM, keeping in mind that you can play around with torque and RPM a bit, depending on the gear that you choose (recall the gear radius we described earlier). However, such a motor may be difficult to find, and so we turn to the advertised performance curves:
http://lancet.mit.ed...rs/motors3.html
(Go to section 3.1).
So I'm not sure if you've ever tried this, but you might notice that when you use your fingers to squeeze the shaft of a DC motor while it's operating, it slows down a bit. So this is described on the curve - at "free running RPM", where there's no torque, it spins really fast, but that RPM drops more if you put more torque on it. So another way of looking at the problem is by saying "right, this is how much torque I need", checking the graph, and finding out what RPM you get out of it. If the resulting RPM is fast enough to maintain a reasonable RoF, then yay, we've found a good choice! If not, then probably pick a different gear/motor/gearbox, and see if you can tweak it to get a good-enough RPM.
This can be a bit of a headache though, as I have found with a similar application - your required RPM depends on your gear size, and your torque requirement depends on your gear size, but you might have to adjust your gear size depending on your torque availability, and everything folds in onto one another. Generally speaking, this requires a few iterations of calculations and experimentation with different motors to see what performance you get. If you need more explanation, feel free to ask, my last paragraph on motors probably wasn't that clear.
But I think it's great that you're not just choosing the easy way out!
#12
Posted 05 June 2018 - 06:24 AM
Yep! I did say diameter, but I should've said radius. And come to think of it, length is probably the wrong term for me to use, I should really use radius instead.
So sort of like you said, with a gear of radius 0.06m, and a force of 5N, you would result in a torque of 0.03Nm.
Just to check that we have an intuitive understanding, imagine you have a 1m arm outstretched, and you're holding an item that weighs 5N (so like 0.51kg or so), your muscles would have to generate 1m x 5N = 5Nm of torque to hold the object up. Similarly, with a gear of say, 6cm (or 0.06m) radius, with a force of 5kg (or 49N), we'd need a torque of 49N x 0.06m = 2.94Nm. Usually when speccing motors, people seem to like using kgcm for some weird reason (yuck, using kg as a unit of force), so it'd probably be more appropriate to describe the torque as 5kg x 6cm = 30kgcm. Note that this is the same value as 2.94Nm, just in different units.
TL;DR - (tangential force on spinning thing) x (radius of spinning thing) = (torque of spinning thing)
Now with omega, omega is basically rotation speed in a purer form, since we're using radians instead of rotations, or degrees. Once again, I should've said radius, not length. So like with a wheel, or a gear, if it's rotating at say, 2 radians/second, and it has a radius of 5m, then the surface velocity (the velocity on the surface of the wheel) of that wheel or gear would be 10m/s.
TL;DR - (omega of spinning thing) x (radius of spinning thing) = (surface velocity of spinning thing)
With the motor selection, yep, ideally you'd pick a motor/gearbox combination with an "nominal torque" and "nominal RPM" that's higher than both your required torque and RPM, keeping in mind that you can play around with torque and RPM a bit, depending on the gear that you choose (recall the gear radius we described earlier). However, such a motor may be difficult to find, and so we turn to the advertised performance curves:
http://lancet.mit.ed...rs/motors3.html
(Go to section 3.1).
So I'm not sure if you've ever tried this, but you might notice that when you use your fingers to squeeze the shaft of a DC motor while it's operating, it slows down a bit. So this is described on the curve - at "free running RPM", where there's no torque, it spins really fast, but that RPM drops more if you put more torque on it. So another way of looking at the problem is by saying "right, this is how much torque I need", checking the graph, and finding out what RPM you get out of it. If the resulting RPM is fast enough to maintain a reasonable RoF, then yay, we've found a good choice! If not, then probably pick a different gear/motor/gearbox, and see if you can tweak it to get a good-enough RPM.
This can be a bit of a headache though, as I have found with a similar application - your required RPM depends on your gear size, and your torque requirement depends on your gear size, but you might have to adjust your gear size depending on your torque availability, and everything folds in onto one another. Generally speaking, this requires a few iterations of calculations and experimentation with different motors to see what performance you get. If you need more explanation, feel free to ask, my last paragraph on motors probably wasn't that clear.
But I think it's great that you're not just choosing the easy way out!
Oh, my bad! I figured by 'length' you meant how far the spring must be pulled back!
So, it must be pulled 6cm, which means we need a gear circumference of 6cm (plus some toothless section for the reset, so more like a minimum of 0.8), and since the formula seems to be C=2πr, we need a minimum r of 0.4/π cm, or about 0.13 cm. That's a tiny gear, so I'm probably doing something wrong...
In any case, we're hoping for an angular velocity of 2-4 π/s, or 1-2 full turns per second.
I'm low on time, so I'll review the details again later, but if you can spot the error on gear size (if any), that'd be great!
#13
Posted 05 June 2018 - 08:41 AM
Oh, my bad! I figured by 'length' you meant how far the spring must be pulled back!
So, it must be pulled 6cm, which means we need a gear circumference of 6cm (plus some toothless section for the reset, so more like a minimum of 0.8), and since the formula seems to be C=2πr, we need a minimum r of 0.4/π cm, or about 0.13 cm. That's a tiny gear, so I'm probably doing something wrong...
In any case, we're hoping for an angular velocity of 2-4 π/s, or 1-2 full turns per second.
I'm low on time, so I'll review the details again later, but if you can spot the error on gear size (if any), that'd be great!
No worries! I wasn't too clear about that.
I think you meant r = 4cm/π, instead of 0.4cm/π which should be 1.3cm radius, that seems about right! The angular velocity also seems reasonable.
#14
Posted 05 June 2018 - 04:53 PM
No worries! I wasn't too clear about that.
I think you meant r = 4cm/π, instead of 0.4cm/π which should be 1.3cm radius, that seems about right! The angular velocity also seems reasonable.
Gah, of course! So we need a motor pulling off a torque of 1.3cm * 5kg or 0.013m*5kg or 0.065 kg M or 0.64 Nm, which seems unreasonably low, but I could be wrong there.
And it needs to do that at 60-120 RPMs (or 6.3-12.6 rads/s)
So its stalling torque should be over 0.64Nm and its rads/sec over 6.3-12.6.
Judging by section 3's bottom from the link, that means I want a maximum power on the motor of 4.03-8.06 ...units. What should the units be, for N*m*rad/sec?
And how does that translate to label characteristics for a motor?
#15
Posted 12 June 2018 - 12:19 PM
Gah, of course! So we need a motor pulling off a torque of 1.3cm * 5kg or 0.013m*5kg or 0.065 kg M or 0.64 Nm, which seems unreasonably low, but I could be wrong there.
And it needs to do that at 60-120 RPMs (or 6.3-12.6 rads/s)
So its stalling torque should be over 0.64Nm and its rads/sec over 6.3-12.6.
Judging by section 3's bottom from the link, that means I want a maximum power on the motor of 4.03-8.06 ...units. What should the units be, for N*m*rad/sec?
And how does that translate to label characteristics for a motor?
Oop, I totally forgot about this, sorry about the late reply.
So, consider the old MTB rhino's datasheet:
https://d13z1xw8270s...nospecsheet.png
Stall torque = 21.40mN.m, or 0.0214 Nm, which is about 30 times less than the stall torque you calculated, which IMO seems pretty reasonable.
Furthermore, we have to consider that once you apply a load onto the motor, it'll slow down - you might notice, at the points of maximum efficiency or maximum output, the motor runs at lower than stall torque, and lower than free-running (i.e. maximum) RPM.
The simplest way to source (that I can think of, off the top of my head), would be to just pick the centrepoint of the operating region (i.e. half of max torque, which results in half of max RPM), and use that as your guideline for picking out a motor. Since you calculated operation of "0.64Nm and its rads/sec over 6.3-12.6.", this would mean that your stall torque would be twice of the operating torque, as would your RPM. So you're looking for a motor that pushes about 1.28Nm and 25.2RPM. (This is assuming that we haven't messed up the numbers somehow)
For reference, the units would be watts for power output. Although I'm sure that you might've noticed, the power output of the motor isn't constant, so while it can be a useful way to get the ballpark performance of a motor, it isn't necessarily how you would define what motor you want to get.
#16
Posted 12 June 2018 - 12:41 PM
The simplest way to source (that I can think of, off the top of my head), would be to just pick the centrepoint of the operating region (i.e. half of max torque, which results in half of max RPM), and use that as your guideline for picking out a motor. Since you calculated operation of "0.64Nm and its rads/sec over 6.3-12.6.", this would mean that your stall torque would be twice of the operating torque, as would your RPM. So you're looking for a motor that pushes about 1.28Nm and 25.2RPM. (This is assuming that we haven't messed up the numbers somehow)
For reference, the units would be watts for power output. Although I'm sure that you might've noticed, the power output of the motor isn't constant, so while it can be a useful way to get the ballpark performance of a motor, it isn't necessarily how you would define what motor you want to get.
I'm guessing this should be 1.28 Nm and 25.2 rads/sec, not RPMs (so about 240 RPM).
Which is very handy and concise, but it brings us to the next question: is that a lot? Am I looking at a rather weak and small motor, a little powerhouse, a car engine or what? Haven't actually ever dealt in motors, as I guess is obvious by how much walking through the physics I needed
#17
Posted 13 June 2018 - 04:31 AM
I'm guessing this should be 1.28 Nm and 25.2 rads/sec, not RPMs (so about 240 RPM).
Which is very handy and concise, but it brings us to the next question: is that a lot? Am I looking at a rather weak and small motor, a little powerhouse, a car engine or what? Haven't actually ever dealt in motors, as I guess is obvious by how much walking through the physics I needed
Nice pickup, that was definitely supposed to be 25.2rad/s.
I'd say it's a perfectly acceptable amount; swarmfires and stampedes run off 380-sized motors. Admittedly their gearboxes are a little bit big, but it's not a crazy size. Not to mention, now we have access to neo hellcats, 180 motors with similar operating characteristics (only slightly lower) to the swarmfire/stampede 380s.
For reference, there's a thread discussing the stampede motors, there's even a link to a data collection excel file somewhere in here:
https://www.reddit.c...ng_motor_specs/
#18
Posted 13 June 2018 - 06:32 PM
Nice pickup, that was definitely supposed to be 25.2rad/s.
I'd say it's a perfectly acceptable amount; swarmfires and stampedes run off 380-sized motors. Admittedly their gearboxes are a little bit big, but it's not a crazy size. Not to mention, now we have access to neo hellcats, 180 motors with similar operating characteristics (only slightly lower) to the swarmfire/stampede 380s.
For reference, there's a thread discussing the stampede motors, there's even a link to a data collection excel file somewhere in here:
You mean this one?
If I'm reading the simplified version correctly, most clock RPMs in the 10s of thousands, way above our 240RPM requirement.
Which is a good thing, since most seem to deliver 2 orders of magnitude under our needed stall torque. Right?
So, we've got 3 orders of magnitude to spare on the RPM, and need 2 orders to back us up on stall torque, so with a 100-150:1 gearbox, it should be able to make it with room to spare. Can one even find such a gearbox?
Also, an online calculator I found seems to be saying this whole thing equates to 30 watts. The complex version lists a "Power out/W" column, which I suppose is the peak wattage of the motor? Cause most don't get 30, but a good handful does.
Edited by Xhosant, 13 June 2018 - 06:37 PM.
#19
Posted 13 June 2018 - 10:58 PM
You mean this one?
If I'm reading the simplified version correctly, most clock RPMs in the 10s of thousands, way above our 240RPM requirement.
Which is a good thing, since most seem to deliver 2 orders of magnitude under our needed stall torque. Right?
So, we've got 3 orders of magnitude to spare on the RPM, and need 2 orders to back us up on stall torque, so with a 100-150:1 gearbox, it should be able to make it with room to spare. Can one even find such a gearbox?
Also, an online calculator I found seems to be saying this whole thing equates to 30 watts. The complex version lists a "Power out/W" column, which I suppose is the peak wattage of the motor? Cause most don't get 30, but a good handful does.
Yep! That's the one.
Yes, you've read it correctly - I might've forgotten to clarify, though, I'm not sure if you've tried opening up a swarmfire or stampede before, but they actually have gearboxes built-in.
I haven't taken a good look at the numbers, but I'll give it a go:
Stampedes on around 7.2V-9V and the stock "2kg" spring (so about 1kg force on average?) achieve about 3 dps (i.e. 180 rpm), if I recall correctly.
The arm radius of the final gear pushing the plunger is about 3cm, I believe, which results in a torque of 1kg*3cm = 3kgcm = 0.29Nm on the whole stampede motor/gearbox setup.
The motor at 9.6V (no gearbox) operates at 20krpm, and 0.0104Nm at peak efficiency, so comparing this with the operation post-gearbox:
20krpm -> 180rpm {111x reduction speed}
0.0104Nm -> 0.29Nm {29x torque increase}
Now, these are super ballpark figures (you might've noticed that my voltage isn't that consistent, 7.2V to like 9.6V is a pretty big range lol), but it seems that your estimation of 100-150:1 seem perfectly reasonable.
With regards to sourcing, I've tried checking out eBay, but for some reason the gearbox numbers aren't advertised too well . I think a good bet would be to check out the gearbox figures on eBay, and the behaviour associated with the yellow gearboxes in XSW kits, then compare them to the motors that they tend to use, and from there, you can estimate the reduction values of the gearboxes. Unfortunately, this does link back to one of the earlier posts, which was pretty much "Just buy some gearboxes and try them until something works!", but now it seems like we've gotten to the point where we do know how to make adjustments from initial tests.
Mind linking the calculator? Power out/W column is likely the mechanical output power, which is the omega*torque thing you managed to calculate a few posts back.
#20
Posted 14 June 2018 - 03:35 AM
Yep! That's the one.
Yes, you've read it correctly - I might've forgotten to clarify, though, I'm not sure if you've tried opening up a swarmfire or stampede before, but they actually have gearboxes built-in.
I haven't taken a good look at the numbers, but I'll give it a go:
Stampedes on around 7.2V-9V and the stock "2kg" spring (so about 1kg force on average?) achieve about 3 dps (i.e. 180 rpm), if I recall correctly.
The arm radius of the final gear pushing the plunger is about 3cm, I believe, which results in a torque of 1kg*3cm = 3kgcm = 0.29Nm on the whole stampede motor/gearbox setup.
The motor at 9.6V (no gearbox) operates at 20krpm, and 0.0104Nm at peak efficiency, so comparing this with the operation post-gearbox:
20krpm -> 180rpm {111x reduction speed}
0.0104Nm -> 0.29Nm {29x torque increase}
Now, these are super ballpark figures (you might've noticed that my voltage isn't that consistent, 7.2V to like 9.6V is a pretty big range lol), but it seems that your estimation of 100-150:1 seem perfectly reasonable.
With regards to sourcing, I've tried checking out eBay, but for some reason the gearbox numbers aren't advertised too well. I think a good bet would be to check out the gearbox figures on eBay, and the behaviour associated with the yellow gearboxes in XSW kits, then compare them to the motors that they tend to use, and from there, you can estimate the reduction values of the gearboxes. Unfortunately, this does link back to one of the earlier posts, which was pretty much "Just buy some gearboxes and try them until something works!", but now it seems like we've gotten to the point where we do know how to make adjustments from initial tests.
Mind linking the calculator? Power out/W column is likely the mechanical output power, which is the omega*torque thing you managed to calculate a few posts back.
http://www.wentec.co...ower_torque.asp
Well, I suppose building the gearbox out of gears isn't that tough. You'd need perhaps 2 pairs of gears, at half and 6 cm or 1 and 12 cm (since the square root of 150 is 12ish, that's the size ratio we want to be fine with just 2 pairs), link one pair on an axle and the other 2 on independent axles. Then, I guess the springer-pusher gear gets attached to the big 'outer' gear while the motor goes on the small one. Might get slightly bulky, but who cares?
#21
Posted 14 June 2018 - 04:31 AM
http://www.wentec.co...ower_torque.asp
Well, I suppose building the gearbox out of gears isn't that tough. You'd need perhaps 2 pairs of gears, at half and 6 cm or 1 and 12 cm (since the square root of 150 is 12ish, that's the size ratio we want to be fine with just 2 pairs), link one pair on an axle and the other 2 on independent axles. Then, I guess the springer-pusher gear gets attached to the big 'outer' gear while the motor goes on the small one. Might get slightly bulky, but who cares?
I'm personally not familiar with the actual implementation of building gearboxes, but if it's something you're comfortable with doing, by all means!
I don't think there is much documentation on gear manufacture within the hobby (that I know of), so I think it'd be an excellent content addition, regardless of how well/janky/clean it ends up being.
#22
Posted 14 June 2018 - 09:27 AM
I'm personally not familiar with the actual implementation of building gearboxes, but if it's something you're comfortable with doing, by all means!
I don't think there is much documentation on gear manufacture within the hobby (that I know of), so I think it'd be an excellent content addition, regardless of how well/janky/clean it ends up being.
It shouldn't be all that complicated. the principles are quite simple. I'm more worried about finding/making a casing than the actual gears
0 user(s) are reading this topic
0 members, 0 guests, 0 anonymous users