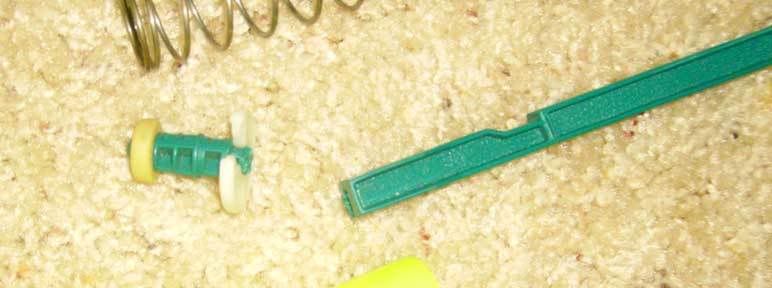
Thanks in advanced for your help.
Posted 05 May 2008 - 07:18 PM
Posted 05 May 2008 - 07:28 PM
Posted 05 May 2008 - 07:30 PM
Posted 05 May 2008 - 07:44 PM
Edited by Rover, 05 May 2008 - 07:45 PM.
Posted 05 May 2008 - 08:40 PM
Posted 05 May 2008 - 08:46 PM
If you are intent on using the stock plunger, may I suggest attemping to create another plunger rod out of polycarbonate and then holding the stock head on with a some kind of fastening device?
I'd recommend screwing it in from the front, and then epoxy-ing the crap out of it, as it will probably have some exposed threads.
Posted 05 May 2008 - 08:47 PM
Yeah, just do that, I've seen people drill theres in, with a right size screw, and they held perfectly well. I think.I'd recommend screwing it in from the front, and then epoxy-ing the crap out of it, as it will probably have some exposed threads.
Posted 05 May 2008 - 08:47 PM
Posted 05 May 2008 - 08:48 PM
I can make you a custom plunger if you want. PM for details.
There is no real solution to fixing this. Anything will eventually break overtime causing frustration. A homemade plunger is your best bet.
Posted 05 May 2008 - 08:54 PM
Edited by Galaxy613, 05 May 2008 - 08:54 PM.
Posted 05 May 2008 - 10:07 PM
Posted 05 May 2008 - 10:23 PM
Edited by ChiliPepperFender, 05 May 2008 - 10:37 PM.
Posted 05 May 2008 - 11:46 PM
Posted 06 May 2008 - 12:00 AM
Posted 06 May 2008 - 12:06 AM
Epoxy Putty!
Posted 06 May 2008 - 10:10 AM
Posted 06 May 2008 - 10:50 AM
Posted 06 May 2008 - 04:27 PM
IPS Weld-on #3 or #4: This is an extremely useful and effective plastic solvent that fuses ABS, Polycarbonate, and Acrylic together (in any pure combination of the three). Simple brush onto or apply to contact area with syringe then secure pieces together in the final form you want. #3 formula is slightly thicker and faster setting, while #4 is water-thin and sets more securely. #4 is recommended for anything you are trying to make air-tight because it's thin enough to use capillary action to fill all of the gaps between the sheets you are joining together. In order to join sheet edges securely and tightly make sure they are sanded to atleast 400grit level and are straight enough to make a scure bond. You do not have to apply any contact pressure to get a good chemical bond. Over application will lead to ugly, but working joints. Can be applied an reapplied as needed without complications.
It's a good idea to use this in a ventilated area, and while it will not adhere your skin to plastic it WILL create permanent fingerprints. This is a mildly toxic substances so excessive skin contact is not a good idea.
It with also work with butyrates and styrenes, but I have not tested it on polypropylene or polyethylene yet so you'll need to ask a plastics shop about compatability. I do know that it is completely incompatible with all PVC plastic blends so avoid buying ABS/PVC (Kydex T). ABS/PVC is a crappy plastic anyways. If you need a specific solvent for a material, check out the wide range of products available from IPS: http://www.ipscorp.com
Both #3 and #4 (and a whole host of other plastic adhesives) are available from McMaster (page 3229).
To apply Weld-on accurately and safely I recommend using 3ml luer-lock syringes with flexible PTFE tubing "needles".
These can be purchased from medical supply, or through industrial supply catalogs such as McMaster (part #s 7510A651 & 75175A691)
Edited by Nonsense Man, 06 May 2008 - 04:32 PM.
Posted 08 May 2008 - 03:04 PM
0 members, 1 guests, 0 anonymous users