
#176
Posted 23 January 2008 - 10:25 PM
#177
Posted 25 January 2008 - 07:27 PM
The rail system is a standard spaced set of holes that allow you to attach different brackets, either of my design or your own. The brackets themselves are very easy to make since you only need to drill holes at the correct spacing.
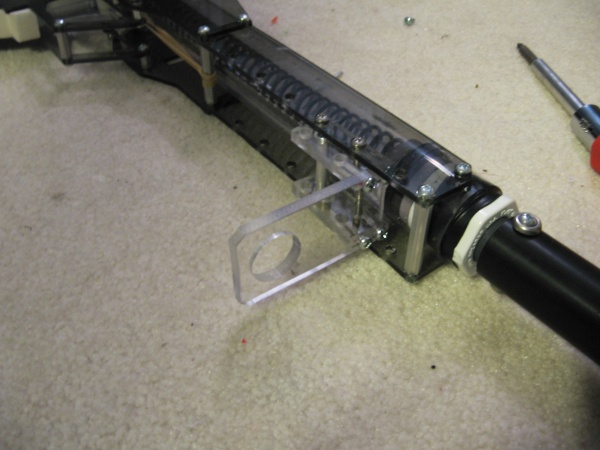
The basic bracket simply have a single hole in the front piece that matches the outer diameter of 1/2 size pipe. You can glue whatever gun internals to the bracket that you want, and that bracket becomes a removable integration module.
The brackets can be attached to the gun using 2-inch length screws (#6, #8, or #10 sizes will all work fine) or with 3/16" diameter quick-release pins.

I still need to take some measurements in order to come up with other standard bracket designs, but these are very easy to make compared to the rest of the gun. I have already used the rail system to make any optional turret attachment. It performed fairly well, but I haven't experimented with it much because I wanted to perfect the slide breech.
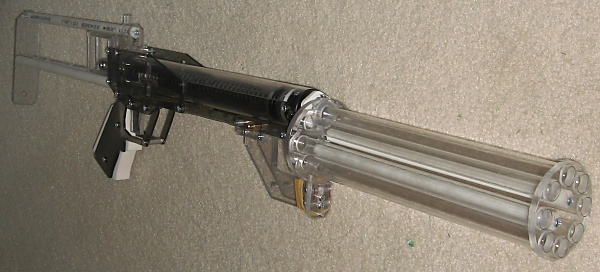
Edited by CaptainSlug, 25 January 2008 - 07:29 PM.
#178
Posted 25 January 2008 - 08:07 PM
We are the proud members of University of Maryland Nerf Activity Society, summer plans are:
Weekly games and summer Dart o' War.
WE LOVE OUTSIDE PLAYERS.
visit www.umdnerf.com for rules and forums or PM me for any questions. We always welcome outside players.
#179
Posted 25 January 2008 - 08:24 PM
#180
Posted 25 January 2008 - 09:00 PM
I might go to work trying to make one of these. I'd like a kit (can't afford the parts for 2-3 +bows) but if I have to, I'll go through hell to make one of these. Seriously. I've been looking for a way to score an xbow cheap for a while, and if I need to make one out of polycarbonate, so be it.
#181
Posted 25 January 2008 - 09:18 PM
At best I would only be able to offer the following items, which are only sold in bulk. So I would be supplying exactly the amount you need in order to save you some money.
Bulk Items ------------------------------------------------------------------ Pre-made Plunger Rod = $3 each 8541K18 - Black Nylon 6/6 Rod 1/2" Diameter = $3.06 for 3 sections cut to required lengths 8541K23 - Black Nylon 6/6 Rod 1" Diameter = $0.25 (for one 3/8 section) 8865K122 - Tear-Resistant Polyethylene Foam Thick Sheet 3/4" Thick, Plain Back, Gray, Pre-cut Grip shape = $1 Each (also available in White or Pink) 5308T347 - Hard Buna-N O-Ring AS568A Dash Number 316 - $0.15 for 2 9637K26 - Continuous-Length Compression Spring Spring-Tempered Steel, 11" L, .844" OD, .08" Wire - $2.50 each 9657K39 - Steel Compression Spring Music Wire, 1" L, 1/4" OD, .020" Wire Diameter = $0.50 each 90402A144 - Zinc-Plated Steel Pan Head Phil Machine Screw External Washer, 6-32 Thread, 1/4" Length = $0.55 per 10 90402A146 - Zinc-Plated Steel Pan Head Phil Machine Screw External Washer, 6-32 Thread, 3/8" Length = $2.65 per 50 90272A159 - Zinc-Pltd Stl Pan Head Phillips Machine Screw 6-32 Thread, 2" Length = $0.60 per Pack of 10 90272A153 - Zinc-Pltd Stl Pan Head Phillips Machine Screw 6-32 Thread, 1" Length = $0.30 per pack of 10 90631A007 - Grade 2 Hex Nylon-Insert Locknut Zinc-Plated Steel, 6-32 Screw Sz, 5/16" W, 11/64" H = $0.15 for 2 90295A075 - Nylon 6/6 Flat Washer #6 Screw Size, .140" ID, .313" OD, .057"-.067" Thk = $0.25 per Pack of 10 92778A074 - 18-8 SS Oval Point Socket Set Screw 6-32 Thread, 3/8" Length = Free for 2 Sub Total = $11.96 Labor = $5 Shipping = $5 Total = $21.96But you would still need to order these items from mcmaster
87225K61 - Gray Tinted Polycarbonate Sheet 1/4" Thick, 12" X 12" = $13.53 Each 85805K26 - Gray Tinted Polycarbonate Sheet 1/8" Thick, 12" X 12" = $5.16 Each 8585K43 - Polycarbonate Round Tube 1-1/2" OD, 1-3/8" ID, Clear = $3.48 for one Foot 4880K314 - Std-Wall (Schedule 40) White PVC Pipe Fitting 1" X 1/2" Sz, Pipe End Male X Socket Fem, Hex Bushing = $0.74 Each 90309A154 - Zinc-Plated Brass Unthreaded Round Spacer 3/8" OD, 1/4" Length, #6 Screw Size = $0.57 Each (2) 93505A440 - Aluminum Male-Female Threaded Hex Standoff 1/4" Hex, 1/4" Length, 6-32 Screw Size = $0.49 Each (2) 91780A125 - Aluminum Female Threaded Hex Standoff 1/4" Hex, 3/8" Length, 6-32 Screw Size = $0.34 Each (4) 91780A131 - Aluminum Female Threaded Hex Standoff 1/4" Hex, 3/4" Length, 6-32 Screw Size = $0.44 Each (3) 91780A337 - Aluminum Female Threaded Hex Standoff 1/4" Hex, 1-1/2" Length, 6-32 Screw Size = $0.78 Each (2) Sub Total = $29.39
Supply Total = $51.35
Savings of: $41.46 over having to buy the bulk items
You will still need to buy full-sheet label paper though. I could sell sheets for $0.50 each if requested though.
If there are a few people that need this I might be willing to do so. The only parts I would be offering cut to size are the foam grip core, stock rods and the plunger rod. Offering the plunger rod already cut to size saves an extra $7 since you don't need a larger 1/4" thickness sheet of plastic. You would still have to cut the notches and drill the holes into it. The size of the plunger rod makes it the only part that's easier to make with a table saw.
Edited by CaptainSlug, 26 January 2008 - 01:05 PM.
#182
Posted 25 January 2008 - 09:56 PM
-Nerfer34
You know what... I know it's kinda late... but Props Cole.
-Baghead
#183
Posted 25 January 2008 - 10:00 PM
Edited by CaptainSlug, 26 January 2008 - 01:18 PM.
#184
Posted 25 January 2008 - 10:19 PM
-Nerfer34
You know what... I know it's kinda late... but Props Cole.
-Baghead
#185
Posted 26 January 2008 - 12:54 PM
We are the proud members of University of Maryland Nerf Activity Society, summer plans are:
Weekly games and summer Dart o' War.
WE LOVE OUTSIDE PLAYERS.
visit www.umdnerf.com for rules and forums or PM me for any questions. We always welcome outside players.
#186
Posted 26 January 2008 - 01:02 PM
The plunger rod when assembled is going to fit snugly inside the plunger tube because the O-rings are the precise size for the gap. You will need to add a very generous amount of silicone lubricant to get the plunger rod to move.
I am still willing to make said part if any of you are not having any success with the ones you have made.
Edited by CaptainSlug, 26 January 2008 - 01:11 PM.
#187
Posted 26 January 2008 - 01:07 PM
-Nerfer34
You know what... I know it's kinda late... but Props Cole.
-Baghead
#188
Posted 26 January 2008 - 01:17 PM
Considering that mine are in the plunger tube I'm no longer sure what problem you are having. If you didn't cut the 3/8" section of rod squarely then that might be the source of your difficulty.Okay, so why is it physically impossible for my O-Rings to fit inside the plunger tube then?
I recommend that you not assume that the cut ends that the rod comes with are square either.
I had to choose an o-ring that is one size smaller so that they wouldn't shift around on the plunger head, and so that when stretched their diameter would decrease very slightly for a somewhat looser fit inside the plunger tube.
#189
Posted 27 January 2008 - 12:06 AM
Considering that mine are in the plunger tube I'm no longer sure what problem you are having. If you didn't cut the 3/8" section of rod squarely then that might be the source of your difficulty.Okay, so why is it physically impossible for my O-Rings to fit inside the plunger tube then?
I recommend that you not assume that the cut ends that the rod comes with are square either.
I had to choose an o-ring that is one size smaller so that they wouldn't shift around on the plunger head, and so that when stretched their diameter would decrease very slightly for a somewhat looser fit inside the plunger tube.
I CANNOT GET THE O-RINGS IN THE TUBE WITHOUT SANDING THEM! If the one inch rod was cut with a lathe and perfectly straight, it still wouldn't fit. I don't know... Has anyone else even started on one to help me?
-Edit-
That was a bit angry. My bad. Its just so frustrating.
Edited by General Cole, 27 January 2008 - 12:16 AM.
-Nerfer34
You know what... I know it's kinda late... but Props Cole.
-Baghead
#190
Posted 27 January 2008 - 12:13 AM
Your plunger rod at most could be 1.400" in diameter at the o-rings, which is still within tolerances to allow it to fit inside the 1.375" ID plunger tube.
If you have access to a lathe the fit won't be as tight if you can make a core that's lathed to 15/16" OD and a tad longer than 3/8" in length.
Edited by CaptainSlug, 27 January 2008 - 12:22 AM.
#191
Posted 27 January 2008 - 03:59 PM
If doing this fixes your problem and temporarily allows you to install the plunger rod more easily then it may be a good idea to cut the plunger core piece slightly longer from now on.
I've changed the length of the piece in the write-up to be 7/16" in length rather than 3/8".
#192
Posted 29 January 2008 - 11:20 AM
We are the proud members of University of Maryland Nerf Activity Society, summer plans are:
Weekly games and summer Dart o' War.
WE LOVE OUTSIDE PLAYERS.
visit www.umdnerf.com for rules and forums or PM me for any questions. We always welcome outside players.
#193
Posted 29 January 2008 - 05:26 PM
My plunger core is .44" long, not .375" like I had assumed. If cut shorter it will act to compress the o-rings and increase their OD.was this problem resolved?
#194
Posted 31 January 2008 - 02:46 AM
#195
Posted 31 January 2008 - 08:43 AM
Getting 10 of them cut using a water-jet service would probably run around $600-800. But I would like to make a total of 30 over the next year.
I won't have any trouble affording the CNC router, and I have a long list of other things I can use it for (including actual work for the company where I'm currently employed).
With all I have planned for the next two years the tool will pay for itself fairly quickly.
Edited by CaptainSlug, 31 January 2008 - 12:40 PM.
#196
Posted 31 January 2008 - 12:14 PM
#197
Posted 31 January 2008 - 12:38 PM
Would be very expensive in terms of the amount of material used to do it that way. A more sensible approach would be to use the feature for designing molds for casting new parts.
Edited by CaptainSlug, 31 January 2008 - 12:47 PM.
#198
Posted 31 January 2008 - 12:52 PM
Exactly. There are optional dimensional reading attachments that eventually I could use the basically ray-trace an object directly into CAD, put a block of material on the CNC router, then have it cut a duplicate.
Would be very expensive in terms of the amount of material used to do it that way. A more sensible approach would be to use the feature for designing molds for casting new parts.
Yeah, that's an incredibly exciting, if perhaps not too practical, concept. Weapons that were formerly extinct become perfectly reproducible. I'm not sure I'd be willing to risk the legal issues of selling such reproduction, though.
#199
Posted 31 January 2008 - 01:02 PM
i'd like to see it in action.

Turd stefans. When I pulled these out of the pillow case i was just like, what... the... fuck...
Muker
<!--QuoteEnd--></div><!--QuoteEEnd-->
#200
Posted 31 January 2008 - 01:03 PM
It wouldn't be very feasible to completely reproduce a whole gun. Too many parts to make without having access to injection-molding equipment. I can't think of any whole guns I would want to go through the hassle of doing that for anyways. I'm thinking more along the lines of being able to mold new Manta Ray shells or make unibody shells for common integrations so you can just move the internals over to the new shell.
But we can discuss all of that at a much later date since I don't want to pay for the attachment right now.
Edited by CaptainSlug, 31 January 2008 - 01:17 PM.
3 user(s) are reading this topic
0 members, 3 guests, 0 anonymous users