I was bored, and being a nerd, I started thinking about both physics and Nerf at the same time. If a barrel is too short, the dart spins out. Too long = too much resistance, which leads to poor range. So what exactly IS the ideal barrel length? Not that it really matters to have it down to three decimal places, but it might be cool. I'm about a third of the way there to calculating a formula relating barrel length and air pressure, but I need some help.
The way I figure, once the dart has left the barrel, any excess air pressure will only cause the dart to spin out and lose accuracy, so the ideal length SHOULD be one in which the pressure in the barrel reaches 14.7 psi (pressure @ sea level) just as the dart exits the barrel. The only problem with this is that the results would yield an extremely long barrel length, since the formula neglects the friction of the dart on the brass* barrel.
I have an idea for an experiment to measure the resistance of the dart in the barrel, but I'm not sure how accurate the results would be. I'll try to draw up a flash doc to show you how it would work. In the mean time, anyone have any input?
*For these calculations I assume we are using straightened micro stefans being fired from a home made (Where pressure can be measured) with a brass barrel.
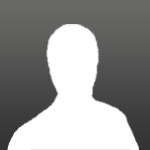
5 replies to this topic
#1
Posted 23 June 2005 - 05:59 PM
"God invented marijuana. Man invented alcohol. Who do you trust more?" -Anon.
#2
Posted 23 June 2005 - 06:02 PM
Well, you'd need the Initial velocity AS the air is coming out behind the dart, and the final velocity when the dart leaves the barrel. Also, you're going to need the weight of the dart, to calculate Fn values, which could be used to calculate the Fk value for friction, after subtracting the two forces (initial and final velocity) to get the value for Fk. From there, you could calculate your Value of Kinetic Friction, which I assume is what you're looking for. I just don't know how to get the velocity.
So you'll need:
Ek=1/2 mv^2
Fk=uk x Fn
I believe that should be all you need... at least to get the force of friction you're looking for. Then again, you actually don't need the last steps I provided, just the difference in inital and final velocities to calculate the change in Ek, which is the friction. However, that's including air friction, unless you have some way to fire it in a vacuum.
And uh, could you send me or something your sm1000 mod... Yeah...
~ompa
So you'll need:
Ek=1/2 mv^2
Fk=uk x Fn
I believe that should be all you need... at least to get the force of friction you're looking for. Then again, you actually don't need the last steps I provided, just the difference in inital and final velocities to calculate the change in Ek, which is the friction. However, that's including air friction, unless you have some way to fire it in a vacuum.
And uh, could you send me or something your sm1000 mod... Yeah...
~ompa
Edited by ompa, 23 June 2005 - 06:05 PM.
#3
Posted 23 June 2005 - 06:59 PM
How about finding the ideal barrel length through observation and a bit of statistics? I've found the ideal nozzle orifice size for water guns with that method.
Essentially, try out a few barrel sizes and record the ranges. Be sure to get multiple trials of each barrel. It would be best to try a few short, medium, and long barrels. Afterwards, use a graphing calculator to enter in the barrel lengths into one list and the ranges in a second list.
Make a Quadratic regression of the two lists, with the barrel lengths as the independent variable. While the actual graph of the ranges and barrel lengths would follow more of a normal curve, the quadratic regression will be accurate enough.
Now all you will need to do to find the best barrel length is find the maximum of the curve. I haven't taken any real math for over a year, but I believe the formula for the maximum of a quadratic equation is -b/2a. You could also graph the quadratic equation and find the maximum that way.
I find methods like this to be fairly accurate for water gun nozzles, but I have not tested them on Nerf barrels given my lack of time and brass.
Essentially, try out a few barrel sizes and record the ranges. Be sure to get multiple trials of each barrel. It would be best to try a few short, medium, and long barrels. Afterwards, use a graphing calculator to enter in the barrel lengths into one list and the ranges in a second list.
Make a Quadratic regression of the two lists, with the barrel lengths as the independent variable. While the actual graph of the ranges and barrel lengths would follow more of a normal curve, the quadratic regression will be accurate enough.
Now all you will need to do to find the best barrel length is find the maximum of the curve. I haven't taken any real math for over a year, but I believe the formula for the maximum of a quadratic equation is -b/2a. You could also graph the quadratic equation and find the maximum that way.
I find methods like this to be fairly accurate for water gun nozzles, but I have not tested them on Nerf barrels given my lack of time and brass.
#4
Posted 23 June 2005 - 08:59 PM
You're not going to find a barrel length that is optimal for both range and accuracy, so lets start with range. As you said, a barrel which results in 14.7 psi (or 1 bar) of pressure as the dart leaves will not yield optimal range because of friction. What you should look for is a barrel where, at the point at which the dart leaves the barrel, the acceleration has reached 0. This ensures that all possible acceleration has taken place and the dart is at its maximum attainable velocity. Acceleration will reach 0 when the force of friction working against the dart is exactly equal to the force due to air pressure behind the dart. This will yield a net force of 0, which according to F=m*a yields a net acceleration of 0. In order to calculate the barrel length, you would have to calculate the pressure required, which requires knowledge of the coefficient of kinetic friction. Unless you want to look up the coefficient of friction between foam backer rod and brass, this will have to be experimentally determined.
Before delving into that, I want to look at the most accurate barrel length, since this is easier. Any difference in pressure between the barrel and the atmosphere at the point when the dart leaves the barrel results in turbulence, which throws off the accuracy of the dart. So in order to maximize accuracy, you are looking at a situation where the pressure inside the barrel should be 1 bar at the point that the dart leaves. This is a significantly easier calculation, since it only requires knowledge of the internal volume of the barrel and the air tank (as well as the pressure after a certain number of pumps). However, a barrel of this length would mean that the dart underwent negative acceleration as the pressure dropped towards 14.7 psi, so you would certainly lose range.
Back to the range-optimizing barrel. I didn't quite understand ompa's idea for determining the coefficient of friction, and I think he's mixing up energy and force. So I'll offer my own method. We can find the energy transferred to the dart by following the formula Kd=.5*m*v^2, where K is kinetic energy of the dart, m is mass, and v is velocity. Take the starting point of the experiment to be the dart sitting in the barrel before the trigger is pulled - the initial Kd is zero. The end point of the experiment will be just as the dart exits the barrel - the maximum kinetic energy. If you know the mass of the dart and the speed as it exits the barrel, you can calculate the final Kd and hence the change in energy over the course of the experiment.
Assuming we can calculate Kd, we now need to break it down into it's parts. Kd is determined by the following equation:
Kd=Ep-Ef
Where Ep is the energy transferred from the pressurized air to the dart and Ef is the energy robbed by friction (or, more accurately, converted to heat). The goal will be to find Ep and hence solve for Ef - if we can find Ef, we can calculate the coefficient of friction.
The energy transferred by the pressure can be calculated using a few basic equations. The first is:
Energy = the integral of Force with respect to distance
You may have seen this in it's non-calculus form, E=F*x. The calculus is necessary because the force of air pressure will change as the dart moves down the barrel (and is hence a function of the distance moved by the dart). The boundaries of the integral will be 0 and y, where y is the distance from the initial position of the dart to the end of the barrel. The next step is to formulate an equation that calculates force as a function of the dart's position in the barrel. The force due to pressure is represented by:
F=P*A, where P is the pressure and A is the area of the surface it is acting upon (in this case the area of the back of the dart). So we now need to find a formula which expresses the Pressure of the air as a function of the dart's position in the barrel. This will be determined by the gas law, which states that as long as the amount of air and the temperature stays the same, the quantity P*V, where P is pressure and V is volume, will be constant. This is expressed as:
(P1)*(V1)=(P2)*(V2)
where P1 and V1 are the initial pressure and volume and P2 and V2 are the final pressure and volume. Rearranging this formula to solve for P2 gives:
(P2)=(P1)*(V1)/(V2)
P1 and V1 will be fixed - the initial pressure and volume of the air tank. V2 will be the volume of the air tank plus the volume of the space in the barrel behind the dart - this will vary as the dart leaves.
So what does this all give us? The integral of (P2)*A with respect to x from 0 to y. If you can follow that you get a cookie.
This will all result in the value for Ep. Now we have Ep and Kd, so we can calculate Ef. The energy sapped by friction is expressed by the formula:
Ef=f*y
Where f is the force due to friction and x is the distance traveled by the dart. Since the force due to kinetic friction is not affected by velocity, you don't need a integral to calculate this. Just divide Ef by y to calculate the force of friction. Now that you have this, you can calculate the pressure necessary to perfectly counter the force of friction - the pressure will allow you to calculate the volume of the barrel, which allows you to set the length to the optimal value.
So it's actually not that hard, assuming you know the internal dimensions of your air tank and barrel, you have a way of testing the pressure of your air tank, you can measure the speed of the dart exiting the barrel, and can perform several tests to verify your results.
Of course, you could use the empirical method that Doom suggested and probably save some time, but this was mainly a thought exercise anyway.
Before delving into that, I want to look at the most accurate barrel length, since this is easier. Any difference in pressure between the barrel and the atmosphere at the point when the dart leaves the barrel results in turbulence, which throws off the accuracy of the dart. So in order to maximize accuracy, you are looking at a situation where the pressure inside the barrel should be 1 bar at the point that the dart leaves. This is a significantly easier calculation, since it only requires knowledge of the internal volume of the barrel and the air tank (as well as the pressure after a certain number of pumps). However, a barrel of this length would mean that the dart underwent negative acceleration as the pressure dropped towards 14.7 psi, so you would certainly lose range.
Back to the range-optimizing barrel. I didn't quite understand ompa's idea for determining the coefficient of friction, and I think he's mixing up energy and force. So I'll offer my own method. We can find the energy transferred to the dart by following the formula Kd=.5*m*v^2, where K is kinetic energy of the dart, m is mass, and v is velocity. Take the starting point of the experiment to be the dart sitting in the barrel before the trigger is pulled - the initial Kd is zero. The end point of the experiment will be just as the dart exits the barrel - the maximum kinetic energy. If you know the mass of the dart and the speed as it exits the barrel, you can calculate the final Kd and hence the change in energy over the course of the experiment.
Assuming we can calculate Kd, we now need to break it down into it's parts. Kd is determined by the following equation:
Kd=Ep-Ef
Where Ep is the energy transferred from the pressurized air to the dart and Ef is the energy robbed by friction (or, more accurately, converted to heat). The goal will be to find Ep and hence solve for Ef - if we can find Ef, we can calculate the coefficient of friction.
The energy transferred by the pressure can be calculated using a few basic equations. The first is:
Energy = the integral of Force with respect to distance
You may have seen this in it's non-calculus form, E=F*x. The calculus is necessary because the force of air pressure will change as the dart moves down the barrel (and is hence a function of the distance moved by the dart). The boundaries of the integral will be 0 and y, where y is the distance from the initial position of the dart to the end of the barrel. The next step is to formulate an equation that calculates force as a function of the dart's position in the barrel. The force due to pressure is represented by:
F=P*A, where P is the pressure and A is the area of the surface it is acting upon (in this case the area of the back of the dart). So we now need to find a formula which expresses the Pressure of the air as a function of the dart's position in the barrel. This will be determined by the gas law, which states that as long as the amount of air and the temperature stays the same, the quantity P*V, where P is pressure and V is volume, will be constant. This is expressed as:
(P1)*(V1)=(P2)*(V2)
where P1 and V1 are the initial pressure and volume and P2 and V2 are the final pressure and volume. Rearranging this formula to solve for P2 gives:
(P2)=(P1)*(V1)/(V2)
P1 and V1 will be fixed - the initial pressure and volume of the air tank. V2 will be the volume of the air tank plus the volume of the space in the barrel behind the dart - this will vary as the dart leaves.
So what does this all give us? The integral of (P2)*A with respect to x from 0 to y. If you can follow that you get a cookie.
This will all result in the value for Ep. Now we have Ep and Kd, so we can calculate Ef. The energy sapped by friction is expressed by the formula:
Ef=f*y
Where f is the force due to friction and x is the distance traveled by the dart. Since the force due to kinetic friction is not affected by velocity, you don't need a integral to calculate this. Just divide Ef by y to calculate the force of friction. Now that you have this, you can calculate the pressure necessary to perfectly counter the force of friction - the pressure will allow you to calculate the volume of the barrel, which allows you to set the length to the optimal value.
So it's actually not that hard, assuming you know the internal dimensions of your air tank and barrel, you have a way of testing the pressure of your air tank, you can measure the speed of the dart exiting the barrel, and can perform several tests to verify your results.
Of course, you could use the empirical method that Doom suggested and probably save some time, but this was mainly a thought exercise anyway.
#5
Posted 24 June 2005 - 09:38 AM
^ That would probably be the way to do it merlinski! I have no way to verify it because I don't know the least about physics.
The only inaccuracy I saw was that 14.7 PSI (atmospheric pressure) doesn't exactly equal 1 bar.
1 bar = 14.5037738 pounds per square inch
1 atm (atmosphere) = 14.6959488 pounds per square inch
You should probably talk in terms of atms due to the slight difference.
The only inaccuracy I saw was that 14.7 PSI (atmospheric pressure) doesn't exactly equal 1 bar.
1 bar = 14.5037738 pounds per square inch
1 atm (atmosphere) = 14.6959488 pounds per square inch
You should probably talk in terms of atms due to the slight difference.
Edited by Doom, 24 June 2005 - 02:18 PM.
#6
Posted 24 June 2005 - 11:20 AM
I'm sorry I have nothing to add but feel compelled to tell merlinski and doom what a nice discussion that was. Both techniques are commendable for determining ideal barrel length although the empirical method is obviously easier (even without graphing).
0 user(s) are reading this topic
0 members, 0 guests, 0 anonymous users