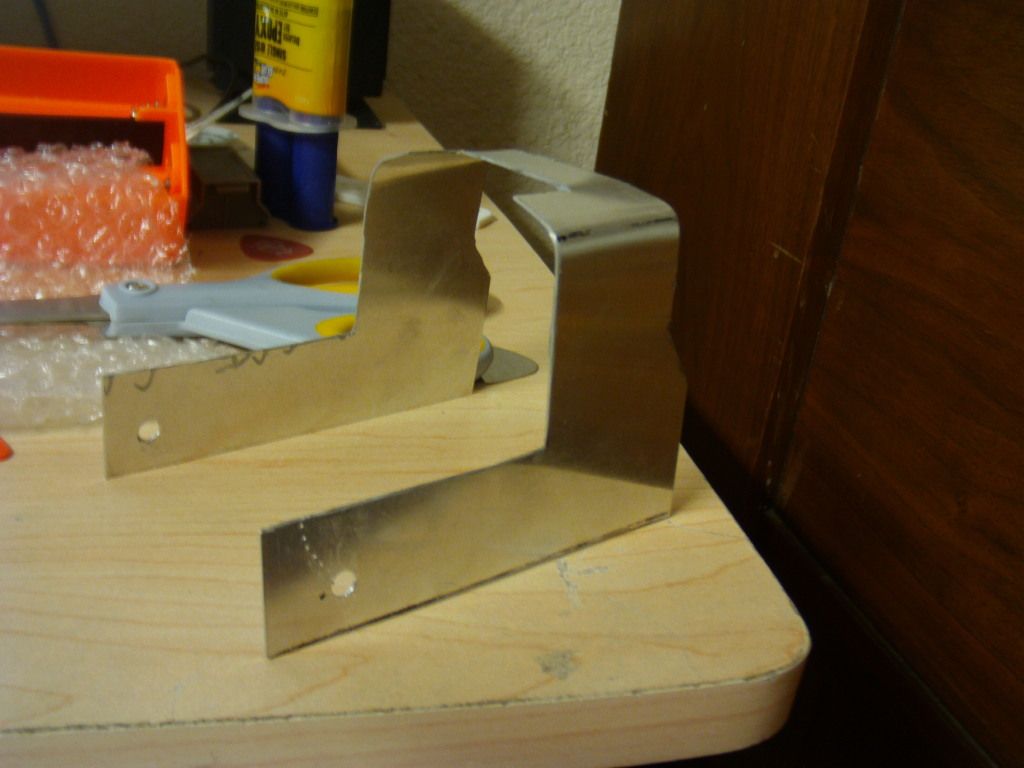
I drilled 2 holes for the priming handle "bar" to feed through, and since I am right handed and prime with my left, i made the right side hole a bit further up so there is always more pressure on the right handle than the left to keep it straight.
Okay here are my problems. One is that when I prime with it on, the top (picture of top will be below) bends when I prime, due to a necessarily thin bar to have enough room to go forward a bit more to not hit the prime indicator and the stock. I have tried to reinforce it, but it seems like I cannot find an epoxy or adhesive to keep extra aluminum reinforcement pieces on it. The bracket is already 0.032" aluminum, but I have to make it thinner since it presses up to the sides of the LS too much (which is another problem). I left extra space up top to add reinforcement.
The second problem is that the holes on the bracket aren't super precise so the bracket tends to rattle. I want to find a sort of washer or spacer to fit onto the bracket, or onto the priming bar to make the fit tighter and make it have a bigger area of contact to the bracket.
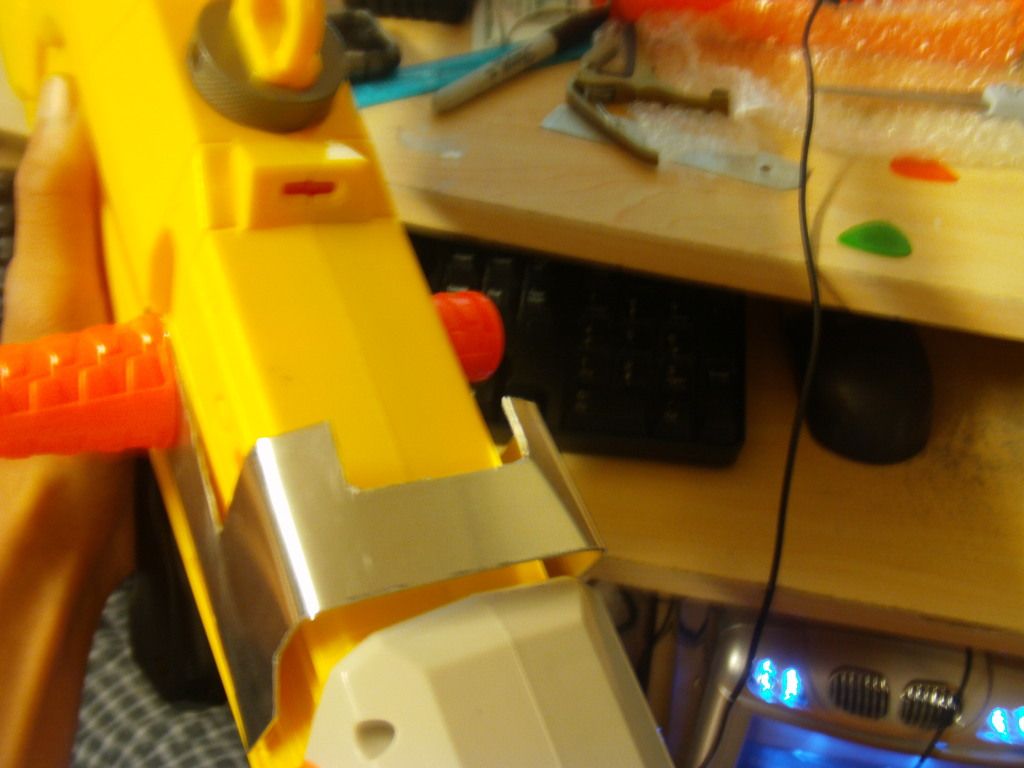
Not primed
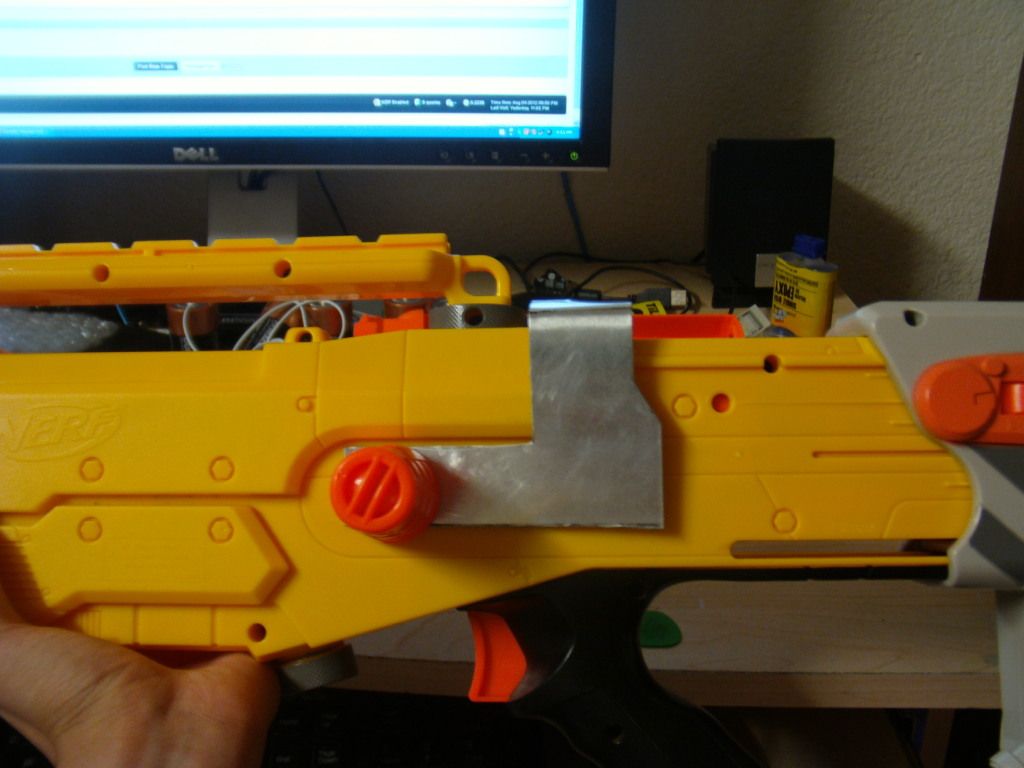
Primed
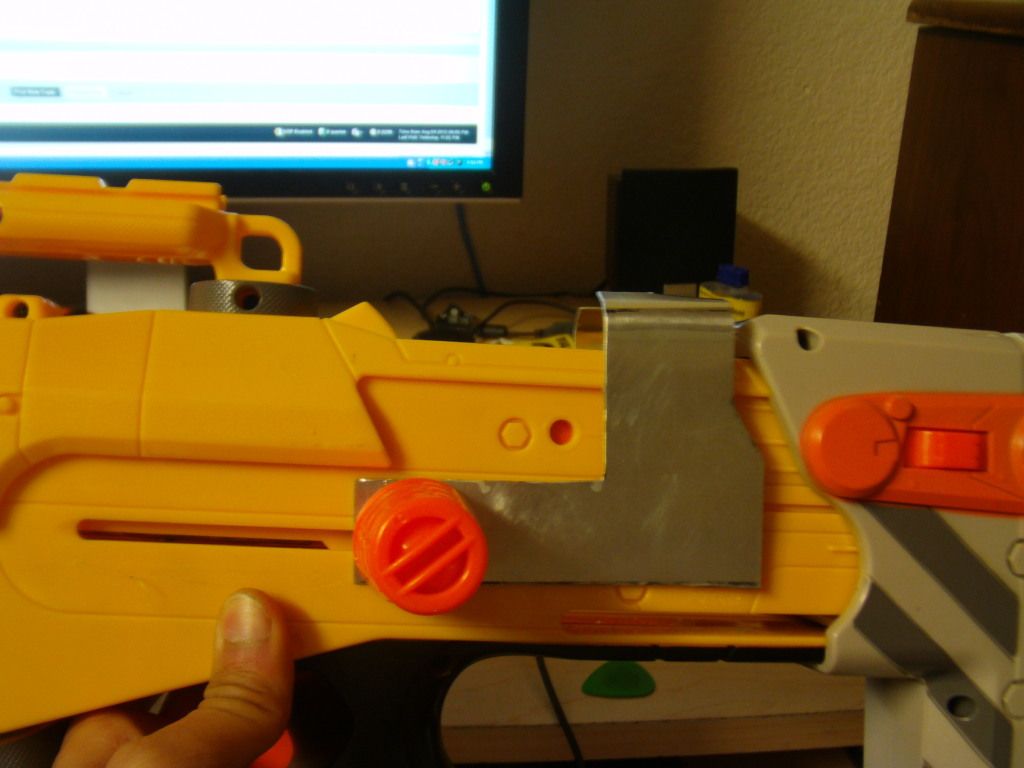